The aerospace industry has always been at the forefront of technological innovation, constantly seeking ways to improve efficiency, performance and sustainability. From rapid prototyping to manufacturing end-use components, ADDere’s additive manufacturing process is transforming how the aerospace sector designs, manufactures and maintains highly complex parts that endure extreme conditions.
Rapid Prototyping & Design Innovation
One of the earliest applications of 3D printing in aerospace was rapid prototyping. Traditionally, prototyping was a lengthy and expensive process, often involving multiple iterations with costly tools and materials. With ADDere, aerospace engineers can quickly produce and test prototypes, drastically reducing development times and costs.
ADDere allows engineers to design and test complex geometries that would be impossible with conventional manufacturing methods. Parts can have intricate features, internal structures, or cooling channels that enhance performance and reduce weight — all of which can be tested in real-time.
The ability to rapidly iterate on designs gives companies the flexibility to experiment with new ideas and refine them before committing to full-scale production, leading to better-performing more efficient aircraft and spacecraft.
Lightweight Structural Airframes & Components
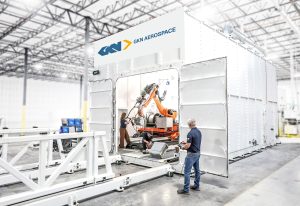
In the aerospace industry, weight reduction is crucial for improving fuel efficiency, reducing emissions and optimizing performance. ADDere is a game-changer in this regard. Unlike traditional manufacturing, which often results in excess material being cut away, ADDere uses an additive process that builds parts layer by layer, minimizing waste and allowing for optimized designs.
Lattice structures and other lightweight geometries can be created with ADDere, reducing the weight of parts without compromising strength. These structures are particularly beneficial for components such as airframes, support structures, mount points and housings, where weight savings can have a substantial impact on overall aircraft performance.
By leveraging 3D printing to produce lightweight yet strong components, aerospace manufacturers can achieve better fuel efficiency, lower operating costs and improved environmental sustainability.
End-Use Aerospace Parts
Perhaps the most exciting application of ADDere’s additive manufacturing process in aerospace is the ability to manufacture end-use parts. Traditionally, metal parts for airplanes and spacecraft were made using traditional manufacturing techniques like casting or machining, which can be time-consuming and expensive. ADDere, however, allows manufacturers to create high-performance, metal parts directly from digital files, which is not only faster but also more cost-effective for complex components.
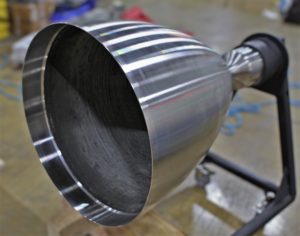
Examples of end-use metal parts produced through 3D printing in aerospace include turbine blades, engine components and structural hardpoints. These parts are critical to the performance of aircraft and spacecraft and must meet the strictest requirements for strength, durability and heat resistance. The ability to print these parts with metals such as titanium, stainless steel and Inconel provides aerospace engineers with unparalleled flexibility in design, material choice and functionality.
Additionally, metal additive manufacturing allows engineers to incorporate internal cooling channels and other innovative features that traditional manufacturing methods cannot achieve. For instance, 3D-printed turbine blades can be designed with intricate internal channels that improve heat dissipation, enhancing engine performance and longevity.
Jet Engine Components
Jet engines are some of the most demanding components in aerospace, requiring materials that can withstand extreme temperatures, high pressures and rapid mechanical stresses. 3D printing has shown particular promise in the production of turbine blades and other jet engine components.
The ability to create complex internal cooling channels is one of the main advantages of 3D printing in engine design. These channels allow for better heat management, which is crucial for maintaining engine performance and durability. For example, a 3D-printed turbine blade can be designed to optimize airflow and cooling, improving fuel efficiency and engine reliability.
Furthermore, 3D printing makes it easier to produce low-volume, highly specialized parts for engine components, which can reduce lead times and costs compared to traditional manufacturing methods.
Spare Parts & Maintenance
One of the most practical applications of additive manufacturing in aerospace is the production of spare parts and components for maintenance and repair. In remote locations or during unscheduled maintenance, sourcing spare parts can be a challenge. However, ADDere allows airlines, maintenance crews and manufacturers to produce replacement parts on demand, significantly reducing downtime and operational costs.
This capability is especially valuable for older aircraft or rare components where traditional manufacturing might not be cost-effective. With ADDere, companies can produce spare parts locally, as needed, without the delays associated with long supply chains.
Additionally, additive repair is gaining traction, where 3D printing is used to repair worn or damaged parts by adding material to specific areas. This technique extends the life of expensive components, reduces waste and lowers the cost of replacement.
Aerospace-Specific Alloys & Materials
Aerospace components are often subjected to extreme conditions, such as high temperatures, corrosive environments and heavy mechanical loads. As a result, the materials used in aerospace manufacturing must be strong, lightweight and durable. ADDere allows manufacturers to produce parts using specialized metal alloys like titanium, Inconel and stainless steel, which are commonly used in aerospace due to their exceptional strength-to-weight ratios and resistance to heat and corrosion.
ADDere also offers the flexibility to design and tailor parts for specific applications, optimizing the material properties for each component. Engineers can select the right material based on the performance requirements of each part, such as heat resistance, fatigue resistance, or corrosion resistance.
Customization & Small-Batch Production
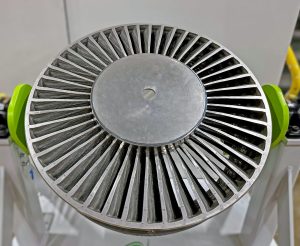
Aerospace companies often require customized parts for specific applications, aircraft models, or mission needs. Whether it’s for a unique aircraft interior, specialized satellite components, or experimental aircraft designs, ADDere provides the flexibility to produce small batches of highly specialized parts without the expense and time investment of traditional manufacturing.
This capability is especially valuable for low-volume production runs where parts are needed in limited quantities but with high precision. Whether it’s custom brackets, structural components, or intricate interior parts, ADDere can provide bespoke solutions for a variety of needs.
ADDere has solutions the aerospace industry depends on
The use of ADDere’s additive manufacturing process in the aerospace industry is not just a passing trend; it’s a technological revolution that’s reshaping how we think about manufacturing. From lightweight structural components to end-use parts and maintenance solutions, metal 3D printing is enabling the aerospace sector to achieve higher levels of performance, efficiency and sustainability.
If you manufacture parts for aerospace, defense, or any other industry then contact us today. ADDere pushes the boundaries of what’s possible and ensures that the skies remain the limit for innovation.