ADDere Large Format System
A Custom Designed System For Printing Large Industrial Parts
The ADDere Large Format System is a production-ready 3D metal printing system that is housed in a custom-built enclosure. The system is a laser-wire additive manufacturing (LWAM) system that achieves the best-in-class metallurgical qualities and material disposition rates with extremely low impurities, all while achieving near net shaped results in the final part.
This custom-designed system has a working envelope of 7 meters long by 3 meters wide and 2 meters tall and can handle a parts payload as heavy as 5,000 kg with room to grow. This system also has the option to utilize many different highly accurate 6 to 12-axis industrial robot configurations, including gantry systems, and a fixed pedestal configuration with a 3-axis coordinated motion workpiece positioner. The ADDere engine system can operate a laser upwards of 30kW and combined with a 500-amp hot wire delivery package provides power for depositing material efficiently. The Large Format System can also weld on both sides of a substrate to allow for the highest additive manufacturing flexibility.
Additionally, an optional inert argon gas environment extends the system’s capabilities to build parts out of Titanium and superalloys such as Inconel. This combined with our specially developed laser head allows for some of the highest deposition rates in the industry.
Along with the physical system, ADDere also provides the software that drives the entire additive manufacturing process. The ADDere Runtime Software controls the build height and width, the energy density control, head mapping and inter-pass print control, and the deposition rate control.
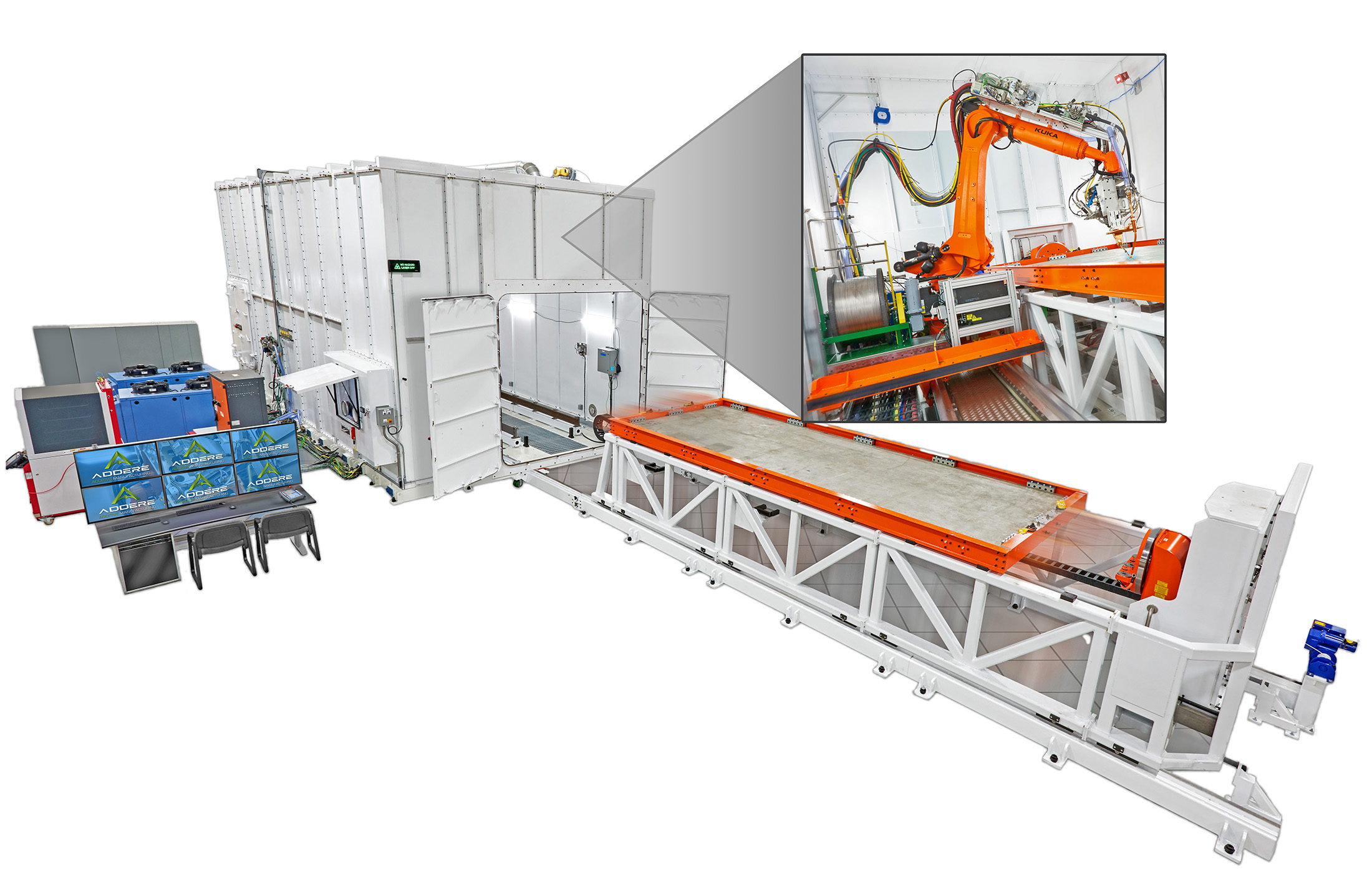
System Specifications
Motion Device Options | 6-Axis Gantry System 12-Axis Robotic Motion System |
Build Part Size (L x W x H) | 7m x 3m x 2m working envelope 3.6-meter hemisphere |
Build Part Max Weight | Up to 5,000 kg including fixturing |
ADDere Engine | 4, 8 & 30 kW Coaxial Engine Laser 20 kW Side Wire Engine Laser |
Laser Head Options | Scanning Head – 4-20+ kW Fixed Focal Spot – 2-20 kW Blown Powder Delivery Head – 2-16 kW |
Wall/Layer Size | Typical 5-6mm pass width and 1-2mm layer height |
Laser Spot Size | 200µm – 20mm |
Sensor System | Real-time, Closed-loop zoom optic with options for coaxial or dithering spot |
Data Collection | Up to 5 samples per second |
Enclosure | Custom-built full laser safety enclosure with options for an inert gas environment. Operator access for consumables without depleting the environment. Option for automation material handling through an anti-chamber. |
Material Delivery | 500-amp hot wire system with power source tracked by closed-loop feedback control |
If you have any additional questions about the ADDere Systems or which system best fits your additive manufacturing applications, please feel free to reach out to us.
do you want to learn more about ADDere's products and services?
From common metals to superalloys
Materials ADDere Prints
Best-in-class Printing Performance
Sample Parts
Turbine Blade
Highly complex stainless steel part that stands 5ft 11in or 1800 layers tall with a height variant of >0.5mm. Learn more ❯
Deposition rate: 4.5 lbs./h
Build time: 30 hours
Material: Duplex Stainless Steel
Equipment used: ADDere Custom System
Rocket Thrust Chamber Assembly
Highly complex seamless stainless steel part that stands 42in tall with a wall thickness of 3mm. Learn More ❯
Deposition rate: 4 lbs./h
Build time: 20 hours
Material: Duplex Stainless Steel
Equipment used: ADDere Custom System
Duplex Stainless Steel Build Plate
Building upon an already finished build plate.
Deposition rate: 23 lbs./h
Build time: 3+ days
Material: Duplex Stainless Steel
Equipment used: ADDere Custom System
Gear
A solid gear made entirely from stainless steel.
Deposition rate: 20 lbs./h
Build time: 10 hours
Material: Stainless Steel
Equipment used: ADDere Custom System
Freeform Design
A demonstration part with a hollow 6mm wall thickness.
Deposition rate: 4.5 lbs./h
Build time: 20 hours
Material: Stainless Steel
Equipment used: ADDere Custom System
Mold Form
Three-hour 3D laser-wire additive build time reduced subtractive processes. The carbon Steel metal printing process allowed customers to move into production faster and more cost-effectively than conventional processes.
Deposition rate: 6 lbs./h
Build time: 3 hours
Material: Carbon Steel
Equipment used: ADDere Standard System
Propeller
Thin-walled metal components are 3D printed onto the existing part. The ADDere additive manufacturing process allows printing onto components built through other means.
Deposition rate: 3 lbs./h
Build time: 4 hours
Material: Carbon Steel
Equipment used: ADDere Standard System
Wing Spar
High-complexity 3D print in titanium. Cross-section aspects of 3D printing reduce construction times and make for a stronger overall part.
Deposition rate: 6 lbs./h
Build time: 1 hour
Material: Titanium Ti64
Equipment used: ADDere Custom System
Cross-section Build
High-complexity 3D print in titanium. Inner detail work makes for ideal additive printing.
Deposition rate: 6 lbs./h
Build time: 1 hour
Material: Titanium Ti64
Equipment used: ADDere Custom System
Titanium Box
High-complexity 3D print in titanium. Inner detail work makes for ideal additive printing.
Deposition rate: 6 lbs./h
Buidt time: 3 hours
Material: Titanium Ti64
Equipment used: ADDere Custom System
Titanium Solid Bar
A solid bar made entirely from Titanium.
Deposition rate: 7 lbs./h
Build time: 6 hours
Material: Titanium Ti64
Equipment used: ADDere Custom System
Part Cladding
Evaluation of the part cladding process.
Deposition rate: 5 lbs./h
Build time: 2 hours
Material: Titanium Ti64
Equipment used: ADDere Custom System