Quality Control
Enhancing Dimensional Quality Control with Contactless 3D Scanning
To ensure the dimensional quality of a part that is printed with our print services, ADDere utilizes a Creaform MetraSCAN 3D optical coordinate measuring machine (CMM). A CMM is the most effective and efficient way to achieve quality assurance by using non-contact 3D scanning technology to ensure dimensional quality control (QC) and print repeatability. It can also help identify and correct any errors, improve efficiency and reduce material waste.
The MetraSCAN 3D is the ideal metrology solution for quality control, quality assurance and part inspection, generating highly accurate dimensional data with any type of component—regardless of part size, material, finish or complexity.
ADDere uses a 3D optical CMM to ensure the following for our customers’ parts:
- First article inspection – Verify that the first sample of a part matches the design specifications and meets the quality requirements
- Dimensional quality inspection – Measures the dimensions of a part and compares them with the nominal values and tolerances
- Defect detection – Identify and locate any defects or deviations in a part, such as cracks, dents, scratches or warping
- Surface analysis – Evaluates the surface quality of a part, such as roughness, texture, definition and variance
If you have any questions about ADDere’s quality control process, please contact us and speak with one of our additive experts.
About the MetraSCAN 3D
ADDere Print Services
Large components operate on their own economies from the high-volume parts made on laser-wire machines. Buying a large-scale additive manufacturing system without testing its abilities can feel like a gamble, especially when there are specialized requirements for the parts to be printed. Sometimes the number of components needed isn’t enough to rationalize the purchase of hardware needed to print the smaller runs. Many times it’s both.
In either case, ADDere understands the situation and provides metal printing as a service to manufacture these components on our machines. Whether to prove our system’s metal additive manufacturing abilities or to run parts without having to invest in 3D printing systems and training, ADDere can print your projects. Learn More…
Next Level Industrial-grade Laser Wire Additive Manufacturing
What's going on at ADDere
Latest Blog Posts
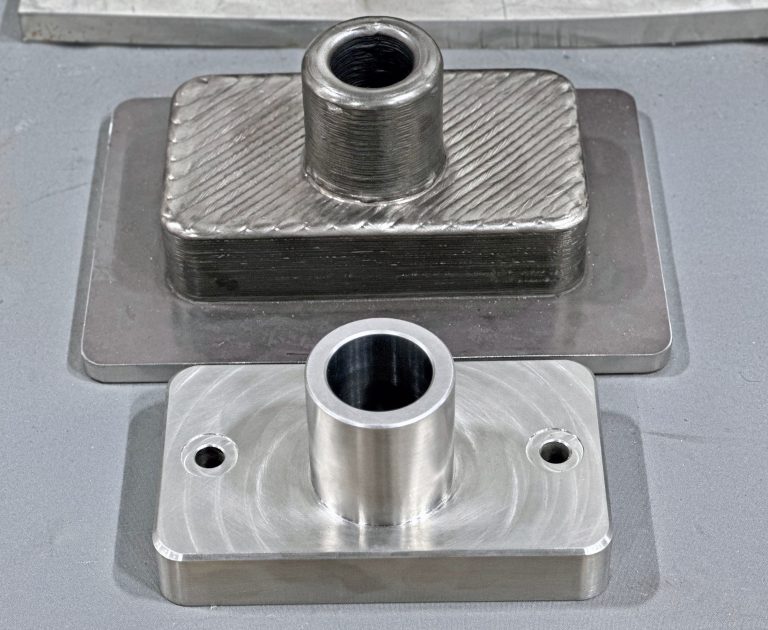
Are 3D Printed Metal Parts Produced with ADDere Strong?
ADDere’s additive manufacturing has revolutionized the production of strong metal-alloy parts, offering unprecedented flexibility and precision. One of the most exciting developments in this field
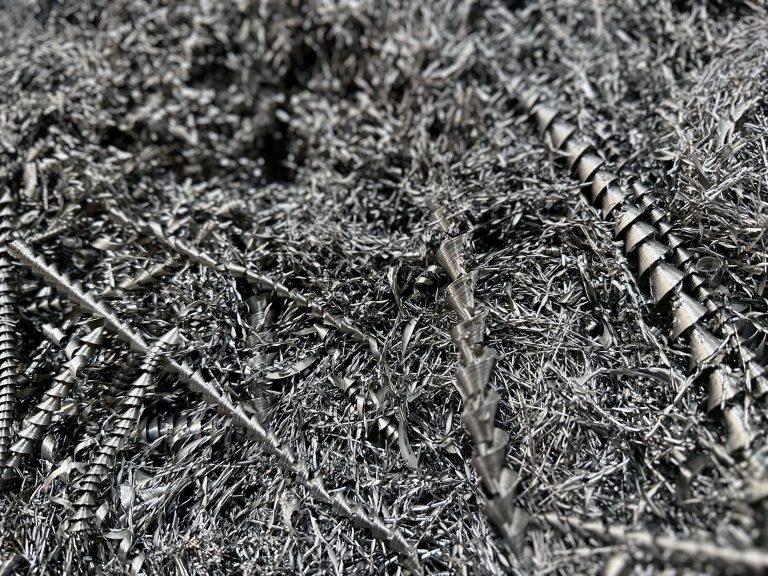
Mitigate Tariffs on Steel by Reshoring Your Manufacturing with ADDere
When it comes to large-scale metal parts manufacturing, ADDere can be a lifesaver for many businesses concerned with high import prices of steel. For decades,
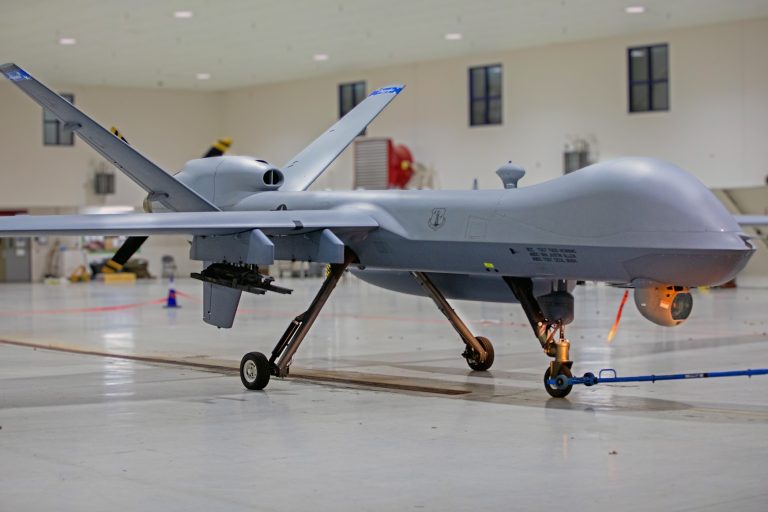
Harnessing ADDere’s Additive Manufacturing Process for Next-Generation Drones
Industrial applications of drones are soaring to new heights in 2025. From utilities and infrastructure inspection to agriculture and defense applications are industries that will
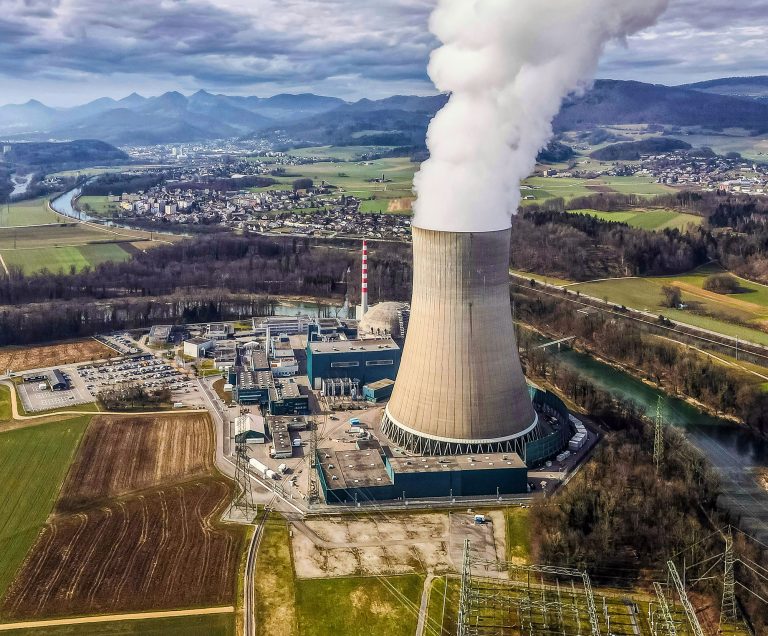
From Concept to Core: How ADDere Transforms Nuclear Reactor Components
Additive manufacturing has been gaining traction in the nuclear energy industry. The development and maintenance of nuclear reactors demand components that meet stringent safety standards
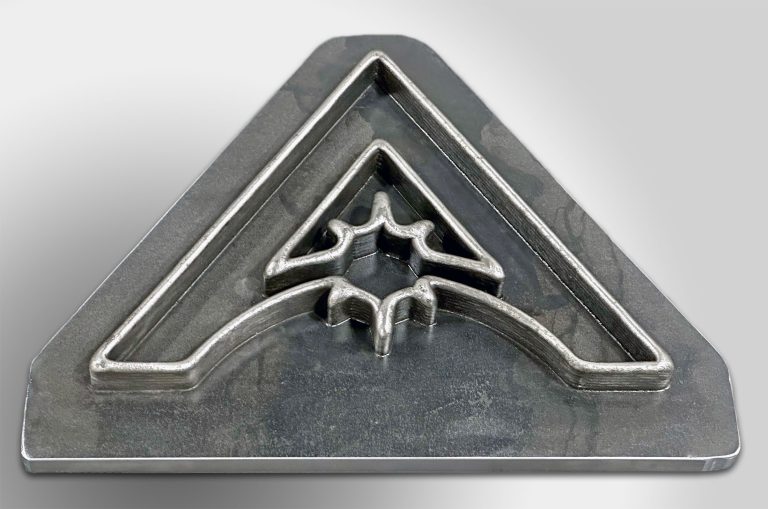
White Paper: The Impact of Additive Manufacturing on Cost, Efficiency & the Future
ADDere’s metal laser-wire additive process is a proven technology for producing complex large-scale metal parts for the defense and aerospace industries. With increasing interest in
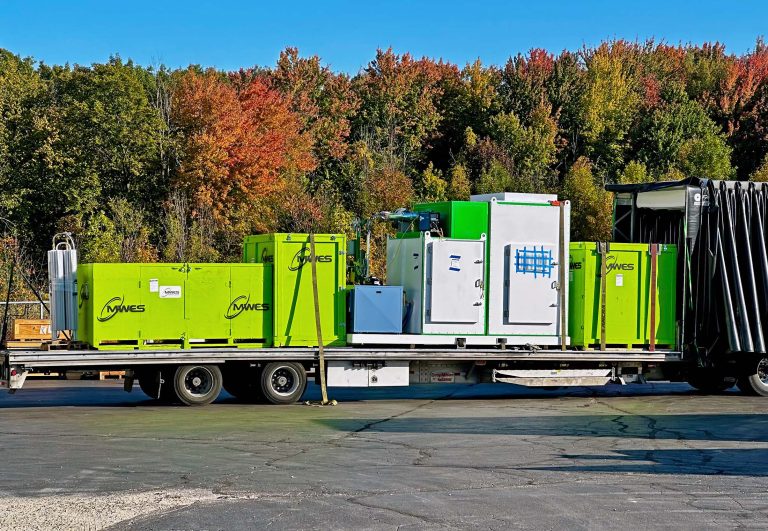
Cost-Benefit Analysis of ADDere’s Additive Manufacturing Process
ADDere’s metal additive manufacturing process has transformed the manufacturing landscape by enabling the production of complex parts with unprecedented precision. Additive manufacturing has evolved from