Titanium
Reduce Time Designing and Building in Titanium
Titanium (Ti-6AI-4V, Ti-6-2-4-2 and CP Ti), known for its high strength-to-weight ratio as well as its thermal qualities has made it a great choice for many aerospace, automotive, power generation and defense applications. The downside of titanium is its workability which typically requires advanced casting processes or fabrications designed to work around its strengths.
The ADDere additive manufacturing system can now streamline the titanium product design, development and production process by directly printing large-scale components in the material, leaving only finish machining. Going directly from CAD to 3D printed parts allows quicker iteration times, ensuring even short-run titanium parts can be quickly tested and fit. Using the ADDere System for production allows for large and complex component designs to be fabricated much faster than conventional methods. The laser-wire additive manufacturing process can produce a near net shaped component ready for final finish machining. This reduces total machining time hogging components from bar stocks and wasted material costs, which opens the door to more efficient and stronger components.
Sample Parts ADDere Prints
Titanium Frame
High-complexity 3D print in titanium. Inner detail work makes for ideal additive printing.
Deposition rate: 6 lbs./h
Buidt time: 3 hours
Material: Titanium Ti64
Equipment used: ADDere Custom System
Cross-section Build
High-complexity 3D print in titanium. Inner detail work makes for ideal additive printing.
Deposition rate: 6 lbs./h
Build time: 1 hour
Material: Titanium Ti64
Equipment used: ADDere Custom System
Titanium Solid Bar
A solid bar made entirely from Titanium.
Deposition rate: 7 lbs./h
Build time: 6 hours
Material: Titanium Ti64
Equipment used: ADDere Custom System
Benefits of ADDere Printed Parts
Titanium has the added benefit of being the strongest metal that can be readily printed in the same manner as 3D printing any form of plastic. This process allows titanium to be fabricated into any shape or part that is deemed necessary for any application. 3D printing titanium is quickly becoming more and more commonplace to the point where it will someday take the place of machining parts.
Titanium has low thermal connectivity making it a difficult metal to traditionally machine making it an ideal candidate for 3D printing. Titanium is a relatively difficult and expensive metal to produce, and machining down tends to waste a great deal of the metal, and thus wasting money in the process. However, the same titanium part that is 3D printed would have a minimal amount of wasted material because it is printed through an additive process. Modern CAD software also has the benefit of optimizing the printing of the final component which can lead to lighter-weight parts while retaining the same strength.
Industrial applications for 3D-printed titanium also include constructing custom replacement parts in the process of refurbishing or repairing older equipment. Doing so keeps those components performing as well as originally intended and extends the life of the machine itself. Titanium replacement parts tend to be sturdier than the original steel parts and thus would reduce the cost of upkeep on older equipment that would otherwise be costly or difficult to replace. Utilizing 3D-printed titanium parts can potentially keep older capable systems operational well past their intended life span.
With its lightweight and overall strength, the manufacturing applications are endless when 3D printing with titanium. In the foreseeable future, 3D printing could become the new go-to standard for manufacturing with titanium.
Industries Where Titanium is Frequently Used
Power Generation & Storage
Aerospace
Aircraft Manufacturing
Automotive
Military & Defense
ADDere’s additive manufacturing can streamline the development and production process of large-scale components made from titanium. Contact us today and see if your manufacturing operations can benefit from ADDere’s additive manufacturing with titanium.
do you want to learn more about ADDere's products and services?
What's going on at ADDere
Latest Blog Posts
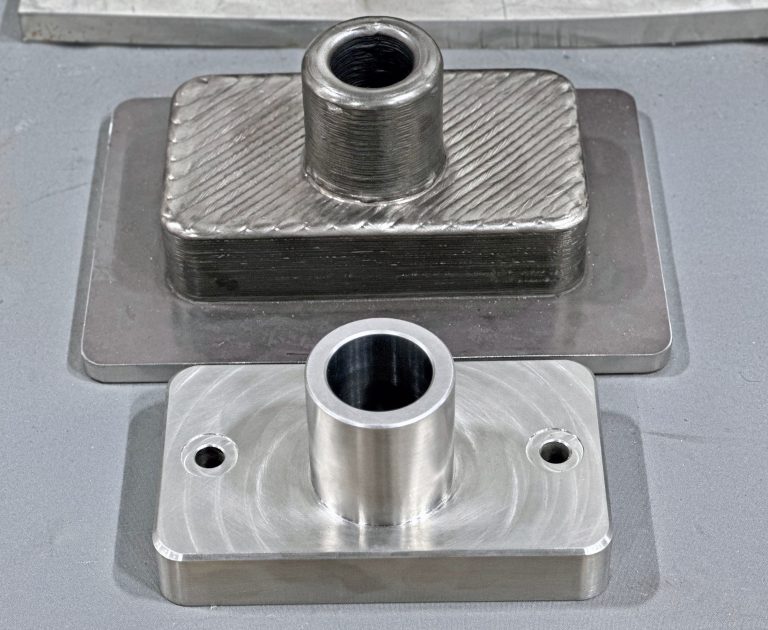
Are 3D Printed Metal Parts Produced with ADDere Strong?
ADDere’s additive manufacturing has revolutionized the production of strong metal-alloy parts, offering unprecedented flexibility and precision. One of the most exciting developments in this field
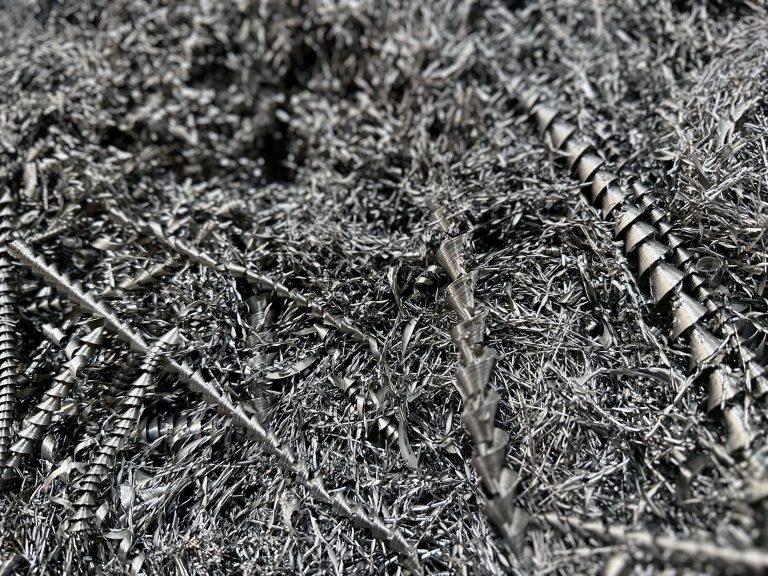
Mitigate Tariffs on Steel by Reshoring Your Manufacturing with ADDere
When it comes to large-scale metal parts manufacturing, ADDere can be a lifesaver for many businesses concerned with high import prices of steel. For decades,
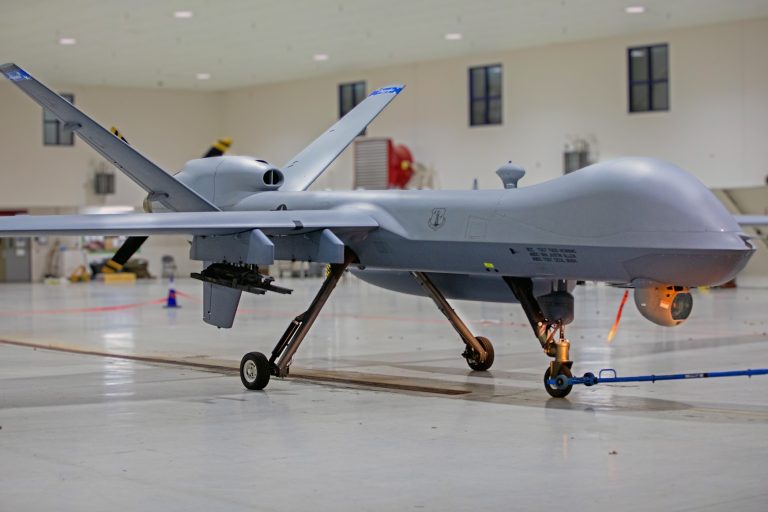
Harnessing ADDere’s Additive Manufacturing Process for Next-Generation Drones
Industrial applications of drones are soaring to new heights in 2025. From utilities and infrastructure inspection to agriculture and defense applications are industries that will
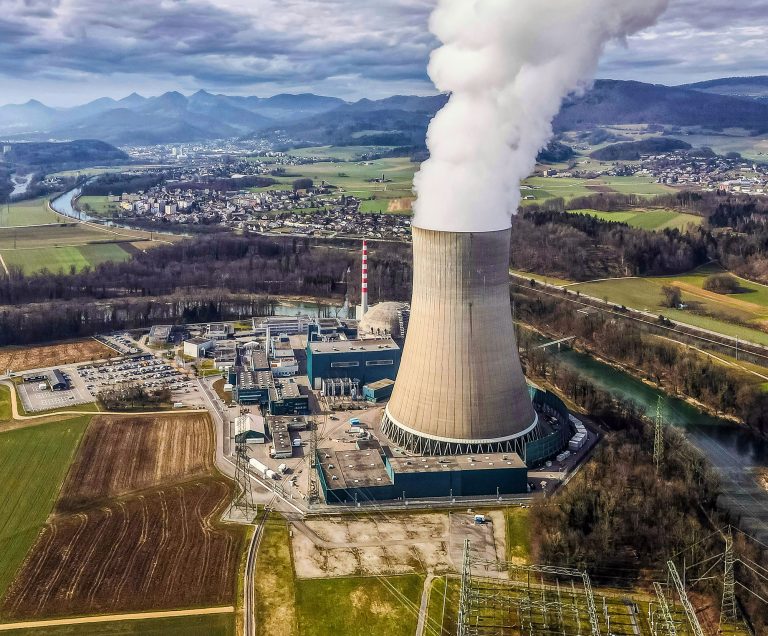
From Concept to Core: How ADDere Transforms Nuclear Reactor Components
Additive manufacturing has been gaining traction in the nuclear energy industry. The development and maintenance of nuclear reactors demand components that meet stringent safety standards
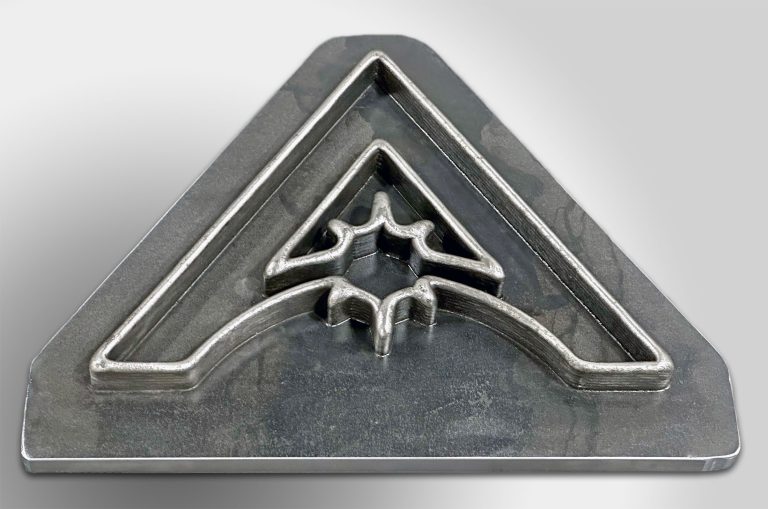
White Paper: The Impact of Additive Manufacturing on Cost, Efficiency & the Future
ADDere’s metal laser-wire additive process is a proven technology for producing complex large-scale metal parts for the defense and aerospace industries. With increasing interest in
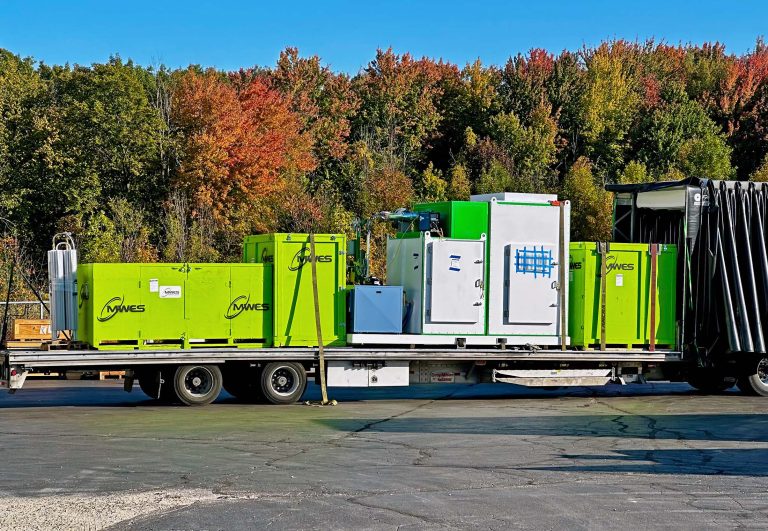
Cost-Benefit Analysis of ADDere’s Additive Manufacturing Process
ADDere’s metal additive manufacturing process has transformed the manufacturing landscape by enabling the production of complex parts with unprecedented precision. Additive manufacturing has evolved from