Refractory Niobium
Print complex metallurgy consistently with ADDere
Refractory Niobium Alloy C103 is utilized in extremely high-temperature applications. Traditional manufacturing processes have a limited pool of suppliers due to feedstock shortages, machining challenges, high buy-to-fly ratios, and high costs. The advantages of ADDere Additive Manufacturing include enhanced characteristics, reproducibility and significant material and time cost and schedule savings in the manufacturing of complicated products. Compared to wrought, Niobium offers greater design flexibility, better mechanical qualities, and a cost saving of an order of magnitude.
Typical Applications for Niobium
Niobium is used in manufacturing various products, such as alloys, tools, dies and superconductive magnets. It is often alloyed with steel to increase its strength, toughness, and resistance to high temperatures and corrosion. It is also used in superconducting materials that can conduct electricity without resistance at very low temperatures. Some examples of niobium applications are jet engines, rockets, nuclear reactors, MRI scanners and particle accelerators.
ADDere’s additive manufacturing can streamline the development and production process of large-scale components made from refractory alloys. Contact us today and see if your manufacturing operations can benefit from ADDere’s additive manufacturing with refractory alloys.
do you want to learn more about ADDere's products and services?
What's going on at ADDere
Latest Blog Posts
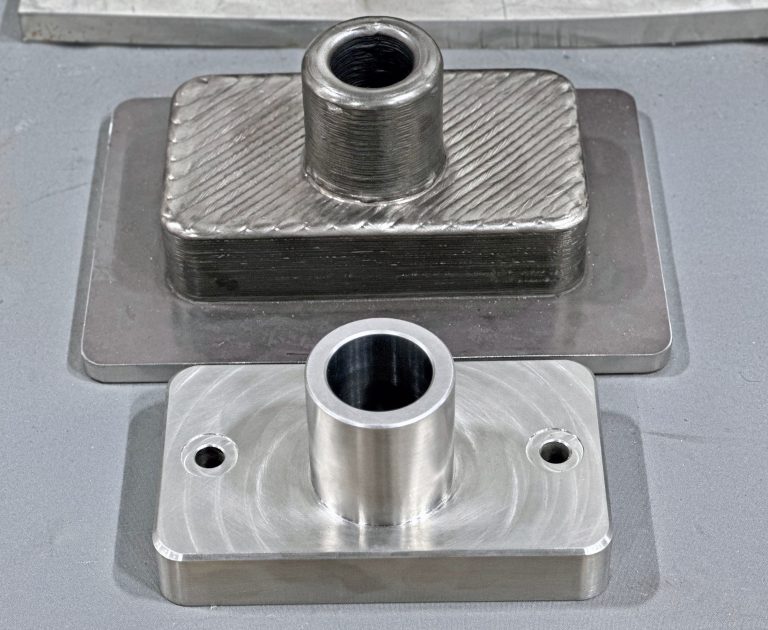
Are 3D Printed Metal Parts Produced with ADDere Strong?
ADDere’s additive manufacturing has revolutionized the production of strong metal-alloy parts, offering unprecedented flexibility and precision. One of the most exciting developments in this field
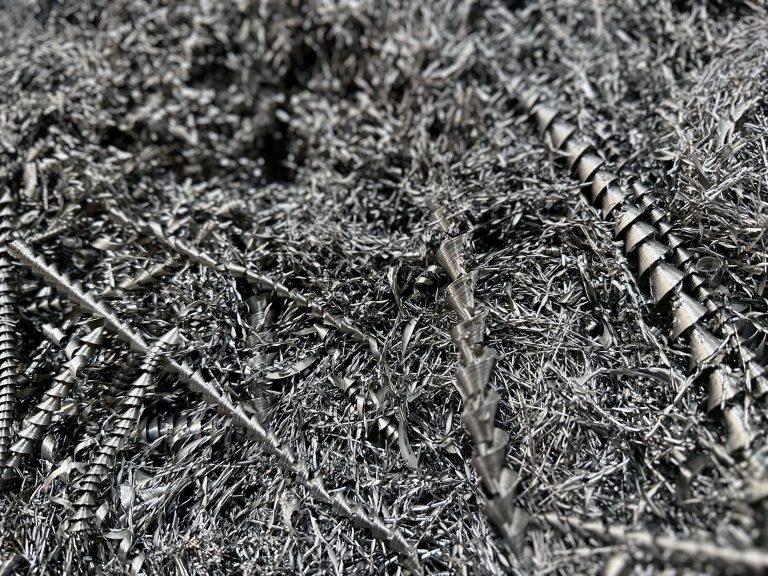
Mitigate Tariffs on Steel by Reshoring Your Manufacturing with ADDere
When it comes to large-scale metal parts manufacturing, ADDere can be a lifesaver for many businesses concerned with high import prices of steel. For decades,
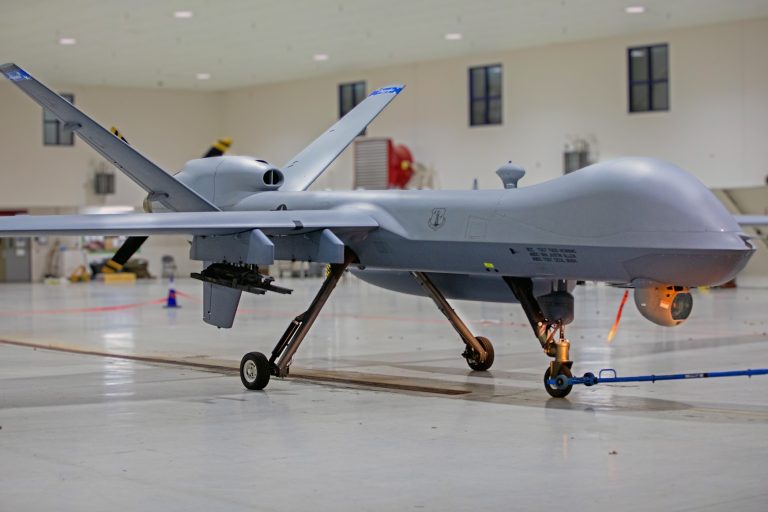
Harnessing ADDere’s Additive Manufacturing Process for Next-Generation Drones
Industrial applications of drones are soaring to new heights in 2025. From utilities and infrastructure inspection to agriculture and defense applications are industries that will
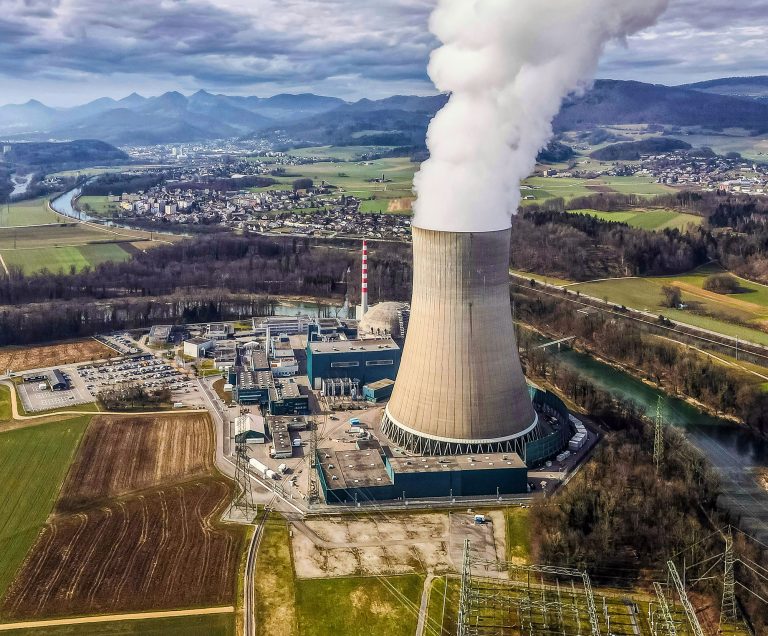
From Concept to Core: How ADDere Transforms Nuclear Reactor Components
Additive manufacturing has been gaining traction in the nuclear energy industry. The development and maintenance of nuclear reactors demand components that meet stringent safety standards
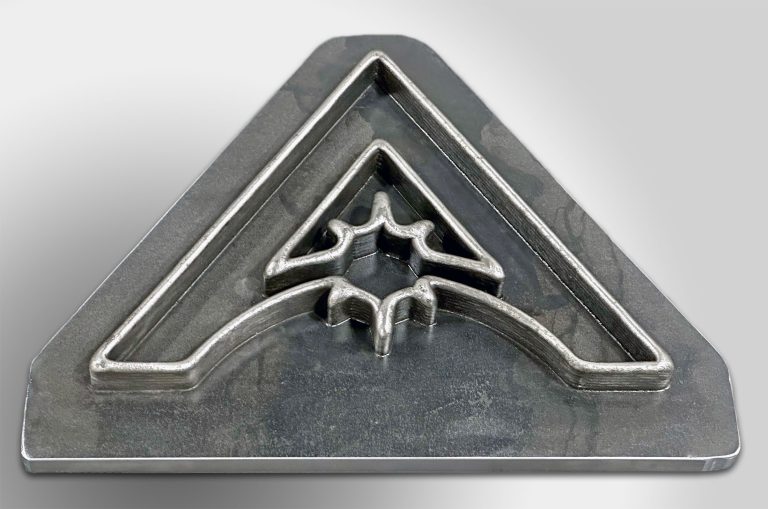
White Paper: The Impact of Additive Manufacturing on Cost, Efficiency & the Future
ADDere’s metal laser-wire additive process is a proven technology for producing complex large-scale metal parts for the defense and aerospace industries. With increasing interest in
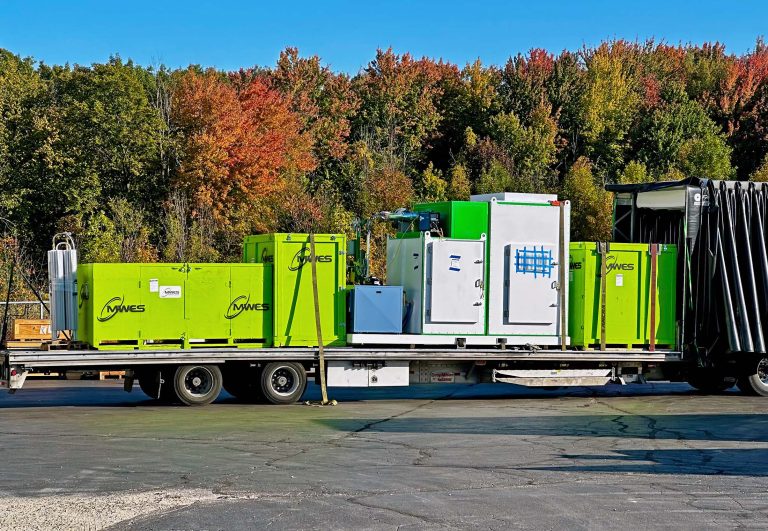
Cost-Benefit Analysis of ADDere’s Additive Manufacturing Process
ADDere’s metal additive manufacturing process has transformed the manufacturing landscape by enabling the production of complex parts with unprecedented precision. Additive manufacturing has evolved from