Invar
Precision instruments benefit from components made of Invar
Invar® 36 is renowned for its remarkably low coefficient of thermal expansion and nickel content that ranges from 36% to 41%. This unique property makes it invaluable in manufacturing applications where precision and stability over temperature changes are crucial. Invar can withstand typical atmospheric and cryogenic temperatures while maintaining good strength which makes it ideal for aerospace applications. Invar’s low expansion rate ensures that these parts retain their dimensions and functionality across a broad range of temperatures.
Curved Plate
A solid curved structure made from Invar.
Deposition rate: 4 lbs./h
Build time: 12 hours
Material: Invar 36
Equipment used: ADDere Custom System
Typical Applications for Invar
Invar is integral in the aerospace industry, used in the construction of aircraft controls and other mechanisms that require exacting tolerances. For instance, it is utilized in the production of components for radio and electronic devices, where consistent performance is essential despite temperature fluctuations. In the realm of optics and laser systems, Invar’s stability helps maintain the alignment of sensitive components. Its versatility extends to the investment casting process, often employed in the manufacture of precision parts for measuring devices, thermostat rods and components for transporting liquefied gases.
For its versatility, it is often employed in the manufacture of precision parts for measuring devices, bimetallic thermostat rods, and components for transporting liquefied gases. The alloy’s low expansion rate ensures that these parts retain their dimensions and functionality across a broad range of temperatures. Invar is used to make optical components, such as lenses, mirrors, and prisms, that need to have precise shapes and sizes. Invar is also used to make electronic components, such as resistors, capacitors, and transistors, that need to have consistent electrical properties. In addition, invar is used to make telecommunication cables and wires, as it can reduce signal loss and interference due to temperature fluctuations. Invar is commonly used where high dimensional stability is required, such as in precision instruments, clocks, seismic gauges, astronomical telescopes, laser systems, capacitor bushings, engine valves and large frame molds.
ADDere’s additive manufacturing can streamline the development and production process of large-scale components made from Invar. Contact us today and see if your manufacturing operations can benefit from ADDere’s additive manufacturing with Invar.
do you want to learn more about ADDere's products and services?
What's going on at ADDere
Latest Blog Posts
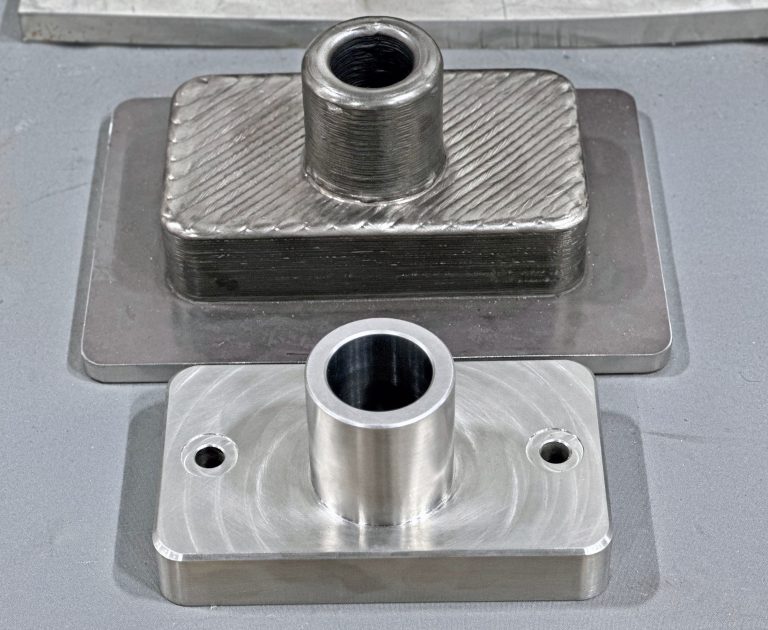
Are 3D Printed Metal Parts Produced with ADDere Strong?
ADDere’s additive manufacturing has revolutionized the production of strong metal-alloy parts, offering unprecedented flexibility and precision. One of the most exciting developments in this field
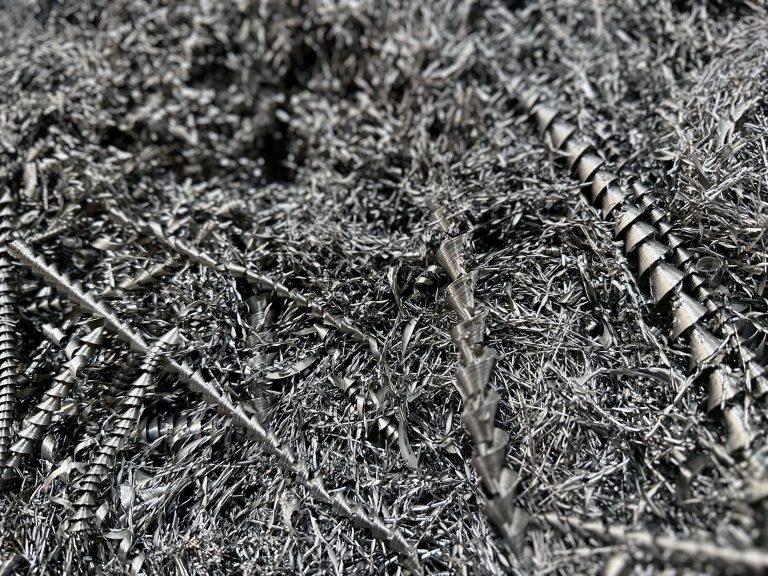
Mitigate Tariffs on Steel by Reshoring Your Manufacturing with ADDere
When it comes to large-scale metal parts manufacturing, ADDere can be a lifesaver for many businesses concerned with high import prices of steel. For decades,
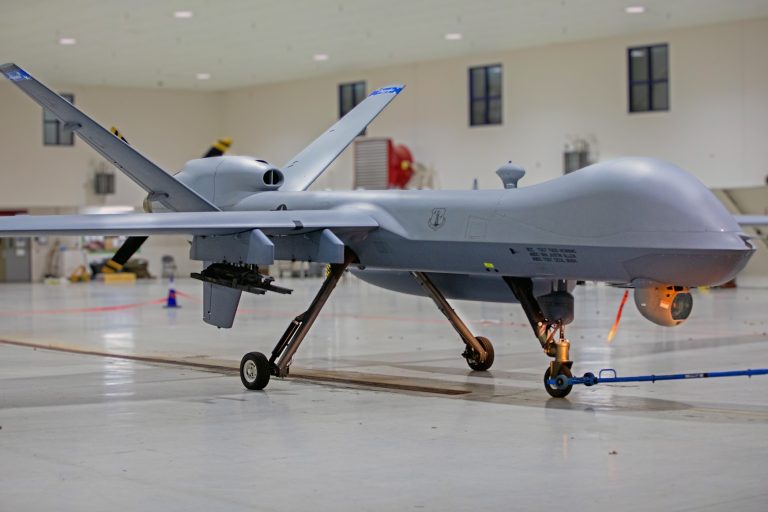
Harnessing ADDere’s Additive Manufacturing Process for Next-Generation Drones
Industrial applications of drones are soaring to new heights in 2025. From utilities and infrastructure inspection to agriculture and defense applications are industries that will
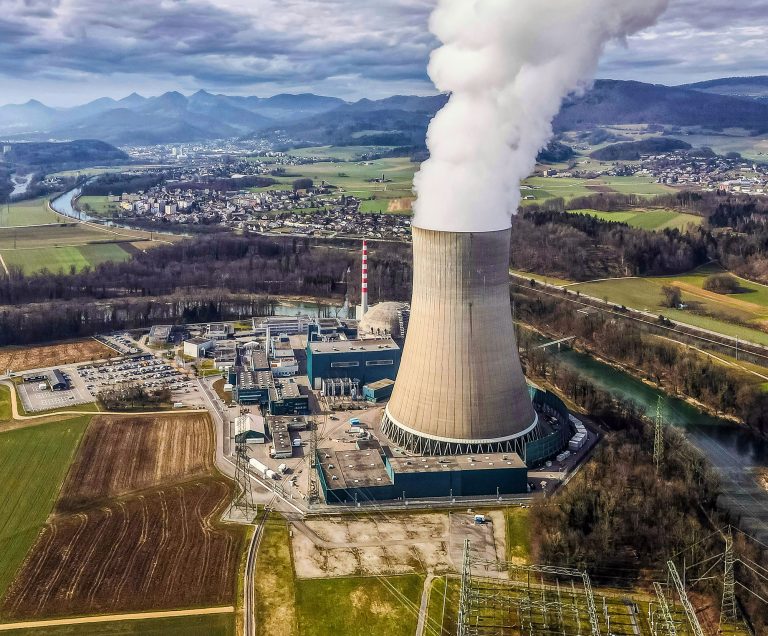
From Concept to Core: How ADDere Transforms Nuclear Reactor Components
Additive manufacturing has been gaining traction in the nuclear energy industry. The development and maintenance of nuclear reactors demand components that meet stringent safety standards
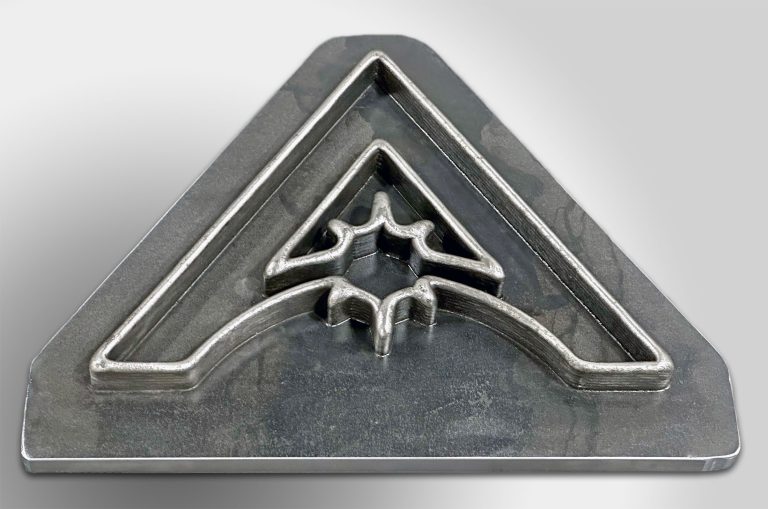
White Paper: The Impact of Additive Manufacturing on Cost, Efficiency & the Future
ADDere’s metal laser-wire additive process is a proven technology for producing complex large-scale metal parts for the defense and aerospace industries. With increasing interest in
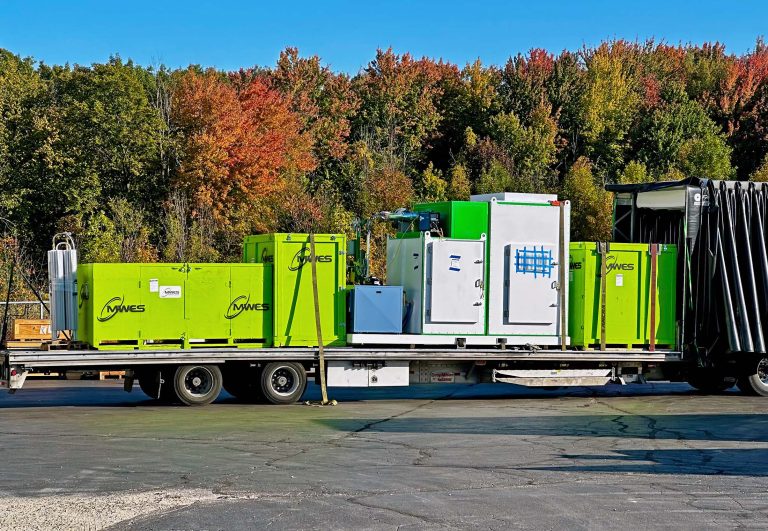
Cost-Benefit Analysis of ADDere’s Additive Manufacturing Process
ADDere’s metal additive manufacturing process has transformed the manufacturing landscape by enabling the production of complex parts with unprecedented precision. Additive manufacturing has evolved from