Oil & Gas Industry
Low-run large-scale 3D metal printing in superalloys with ADDere Additive Manufacturing
One-off components are common in the Oil and Gas industry. The options for these specialized parts are either going through the motions of casting parts or spending large amounts of time either milling or assembling a number of components to get to the one part needed. With the ADDere wire deposition additive manufacturing system, parts can go from CAD directly to casting-level parts ready for final machining without having to make molds, and cores or shop around for a casting plant that can actually pour the part you need.
With a variety of iron-based alloys like duplex stainless steel and nickel-based alloys like Inconel 718 or Alloy X available to print, the ADDere metal 3D printing system allows components that previously leave the shop to get cast, to be done in-house – and with the ability to use much more exotic materials. These materials open up greater resistance to harsh chemicals and conditions and they can be 3D printed at your facility.
The Advantages of Using ADDere 3D Metal Printing in the Oil & Gas Industry
The ADDere additive manufacturing process offers a number of very important benefits to large component manufacturers, like those servicing the Oil & Gas industry. It also offers an alternative to going through the conventional casting process for parts where greater, more consistent quality can be had and typically on shorter timelines.
Below, we’ve broken out some of the larger benefits of using laser wire additive manufacturing in comparison to conventional laser powder additive or casting operations.
Large Size Prints
ADDere’s Laser Wire Additive systems are the perfect process for printing large parts. Our additive manufacturing systems start at build areas of one meter cubed and increase in volume from there, offering the ability to print parts far larger than most SLS systems.
The systems are also able to print high-mass components. ADDere 3D metal printers are designed to put down large amounts of material per hour. That ability translates into more efficiently building parts that have thick side walls and solid features, perfect for high wear and high-pressure applications that need greater amounts of material to be relied upon in the field.
Combining these capabilities allows ADDere to print large valve components and control bodies at the sizes necessary for large installations as one contiguous part, sidestepping the need to use multiple prints to build a component other additive manufacturing methods require.
High-Quality Deposition
Several aspects of the additive process ADDere uses are instrumental in guaranteeing best-in-class quality. The use of laser heating in the process offers the best heat control. From a metallurgical standpoint, this highly precise ability to control the heat in the process provides consistency throughout the build. Application of the laser heat also sidesteps many of the issues castings could develop in the pouring process like cold shuts and laps.
ADDere’s ability to print within a completely inert environment further reduces the potential for occlusions or impurities commonly found in the casting process. Cleaner materials mean stronger parts over the life of the component.
Overseeing all of these areas is ADDere’s proprietary closed-loop feedback system that maintains the process as the system prints. Through an array of sensors, the system is able to analyze the crucial aspects of the build and adjust a number of settings several times a second as it deposits materials. This oversight keeps a close watch on the process to ensure the print is properly constructed, both dimensionally as well as internally consistent.
All the Right Metals
ADDere prints with many of the materials the oil & gas industry commonly use in the construction of critical components. With a variety of iron-based alloys like duplex stainless steel and nickel-based alloys like Inconel 718 or Alloy X available to print, the ADDere metal 3D printing system allows components that previously leave the shop to get cast, to be done in-house – and with the ability to use much more exotic materials. These materials provide greater resistance to harsh chemicals and conditions and they can be 3D printed at your facility.
Typical Oil & gas components that ADDere can fabricate
Is ADDere right for you?
If your business is looking to manufacture components for the oil and gas industry from superalloys in a fast, cost-effective way, then contact us today. The ADDere large-scale laser-wire additive manufacturing process can print in sizes and materials to fit your business’s needs.
do you want to learn more about ADDere's products and services?
What's going on at ADDere
Latest Blog Posts
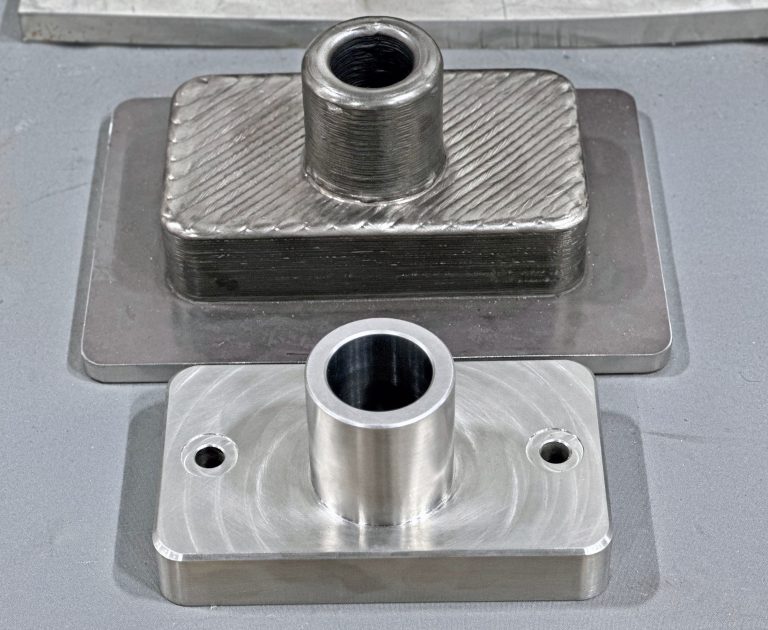
Are 3D Printed Metal Parts Produced with ADDere Strong?
ADDere’s additive manufacturing has revolutionized the production of strong metal-alloy parts, offering unprecedented flexibility and precision. One of the most exciting developments in this field
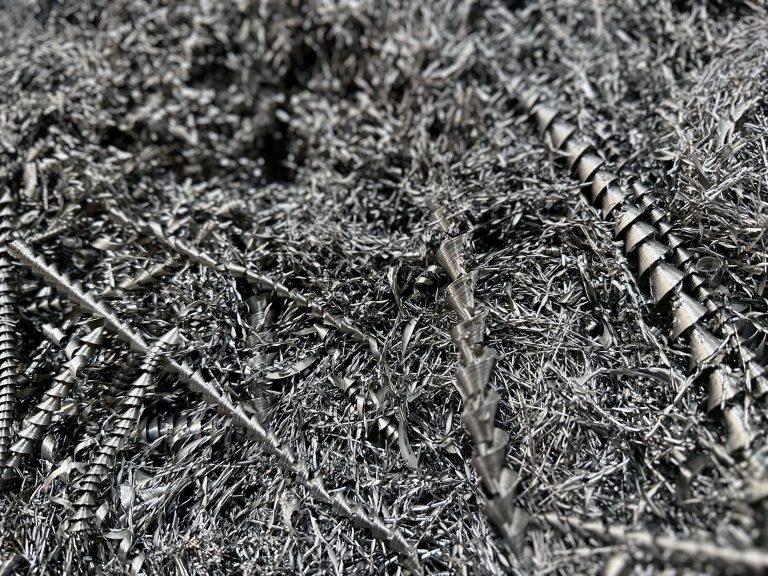
Mitigate Tariffs on Steel by Reshoring Your Manufacturing with ADDere
When it comes to large-scale metal parts manufacturing, ADDere can be a lifesaver for many businesses concerned with high import prices of steel. For decades,
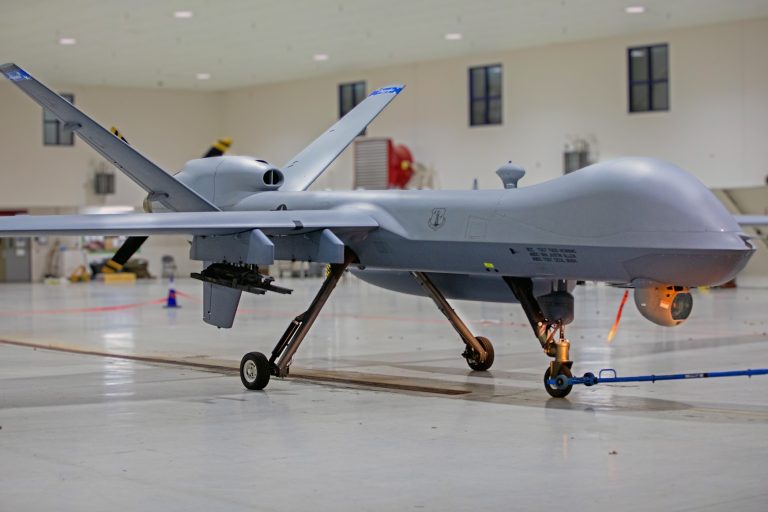
Harnessing ADDere’s Additive Manufacturing Process for Next-Generation Drones
Industrial applications of drones are soaring to new heights in 2025. From utilities and infrastructure inspection to agriculture and defense applications are industries that will
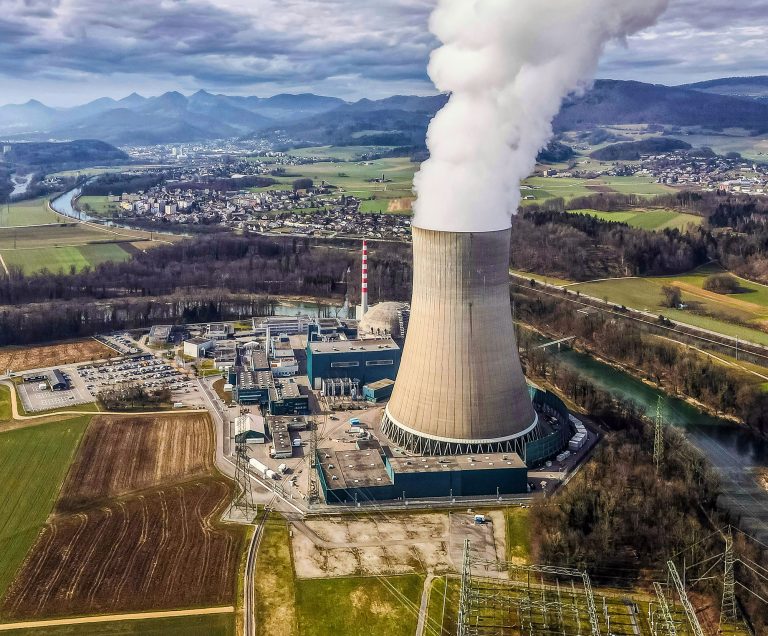
From Concept to Core: How ADDere Transforms Nuclear Reactor Components
Additive manufacturing has been gaining traction in the nuclear energy industry. The development and maintenance of nuclear reactors demand components that meet stringent safety standards
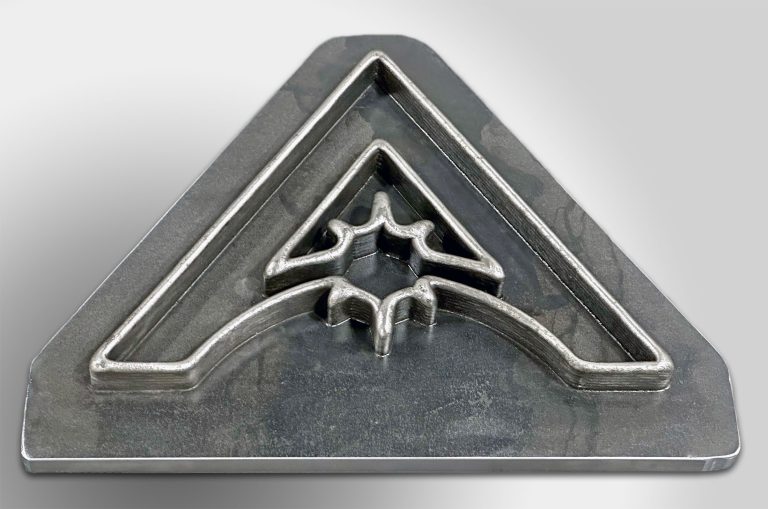
White Paper: The Impact of Additive Manufacturing on Cost, Efficiency & the Future
ADDere’s metal laser-wire additive process is a proven technology for producing complex large-scale metal parts for the defense and aerospace industries. With increasing interest in
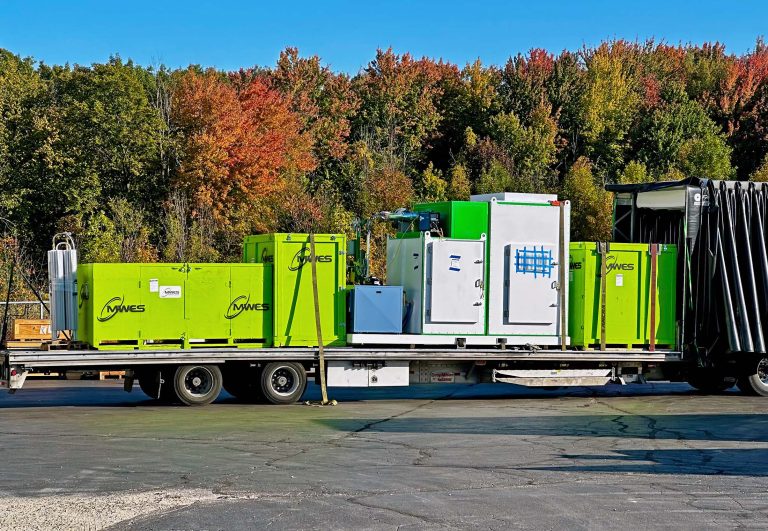
Cost-Benefit Analysis of ADDere’s Additive Manufacturing Process
ADDere’s metal additive manufacturing process has transformed the manufacturing landscape by enabling the production of complex parts with unprecedented precision. Additive manufacturing has evolved from