Defense Industry
3D metal printing opens design opportunities in the military & defense manufacturing industry
ADDere’s metal additive manufacturing is a game-changer for military applications in the defense industry by improving combat readiness, reducing costs, shortening the supply chain and eliminating part obsolescence. With more and more exotic metals being used for protective and structural components as well as high-temperature applications, the need for flexibility in designing these components also increases.
The opportunity to build components with metal wire deposition allows even more shape possibilities that are not available with conventional fabricating processes alone. ADDere allows military vehicle engineers to move past plate-on-plate design thinking without having to resort to expensive shorter-run castings. The ADDere metal 3D printing systems can also move component testing from concept to production-ready much faster, allowing quicker iteration times, regardless of whether the components are desired in a variant of Inconel, titanium or stainless steel.
Enhancing Readiness
One of the key benefits of ADDere additive manufacturing for the Defense Logistics Agency (DLA) is the ability to increase readiness while saving money. By developing common technology, standards and processes, the DLA ensures that the military services can share data and collaborate effectively. This not only enhances operational readiness but also drives cost efficiencies through reduced waste and optimized resource utilization. Additionally, with additive manufacturing, parts can be produced on an as-needed basis, reducing the need for large inventories and storage facilities. This on-demand production capability is particularly beneficial for military operations, where the logistics of transporting and storing spare parts can be challenging.
Supply Chain Simplification
ADDere additive manufacturing systems can simplify supply chains by reducing the number of steps and intermediaries required to produce a part. This simplification leads to increased efficiency and reduced lead times, which are critical in defense manufacturing where time-sensitive deployments are common. Moreover, those parts can be produced locally and on-site including at remote bases or onboard deployed ships.
Repair and Maintenance
The ability to print replacement parts on-site or near the point of use is a significant advantage for military operations. ADDere’s systems enable the repair and maintenance of equipment in the field, reducing equipment downtime and increasing the operational readiness of military units.
ADDere has produced additive systems that construct large-scale titanium aerostructures and stainless steel heavy vehicle engine intake guarding, but the possibilities of ADDere are endless. If you are a components or equipment supplier for the Department of Defense (DOD) or are the logistics or procurement division of the military, then contact us today. ADDere’s custom systems can be scaled up to produce very large components or, if a smaller system is necessary, the ADDere standard system has a footprint that can fit on most shop floors.
Military components that ADDere can Fabricate
Is ADDere right for you?
If your business is looking to manufacture components for the defense industry from superalloys in a fast, cost-effective way, then contact us today. The ADDere large-scale laser-wire additive manufacturing process can print in sizes and materials to fit your business’s needs.
do you want to learn more about ADDere's products and services?
What's going on at ADDere
Latest Blog Posts
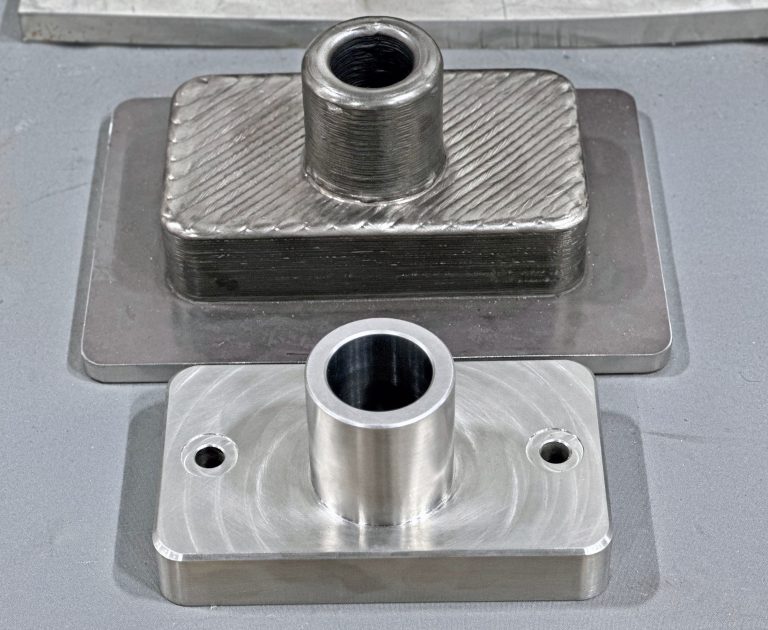
Are 3D Printed Metal Parts Produced with ADDere Strong?
ADDere’s additive manufacturing has revolutionized the production of strong metal-alloy parts, offering unprecedented flexibility and precision. One of the most exciting developments in this field
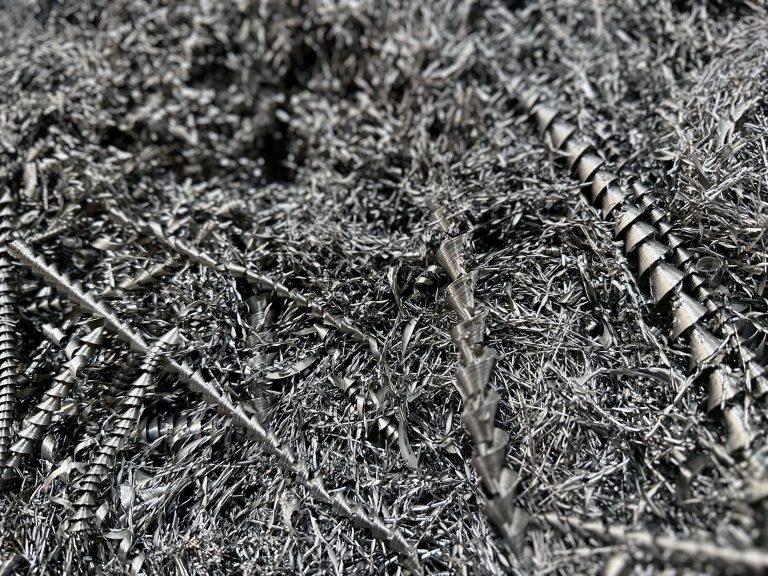
Mitigate Tariffs on Steel by Reshoring Your Manufacturing with ADDere
When it comes to large-scale metal parts manufacturing, ADDere can be a lifesaver for many businesses concerned with high import prices of steel. For decades,
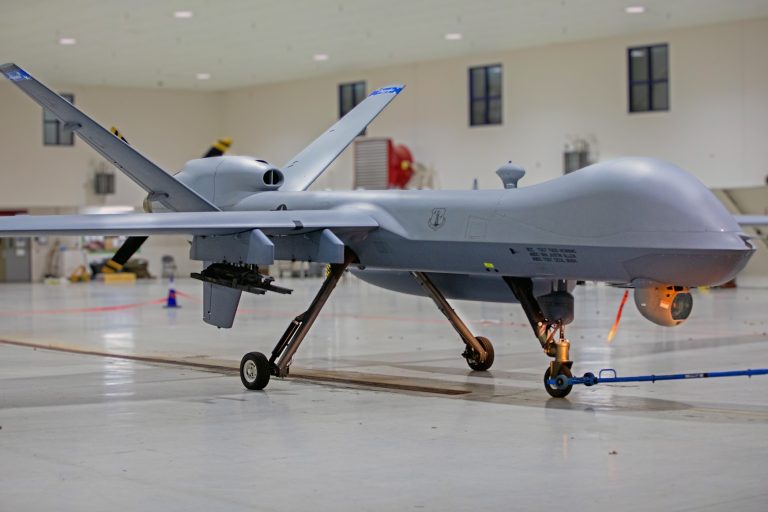
Harnessing ADDere’s Additive Manufacturing Process for Next-Generation Drones
Industrial applications of drones are soaring to new heights in 2025. From utilities and infrastructure inspection to agriculture and defense applications are industries that will
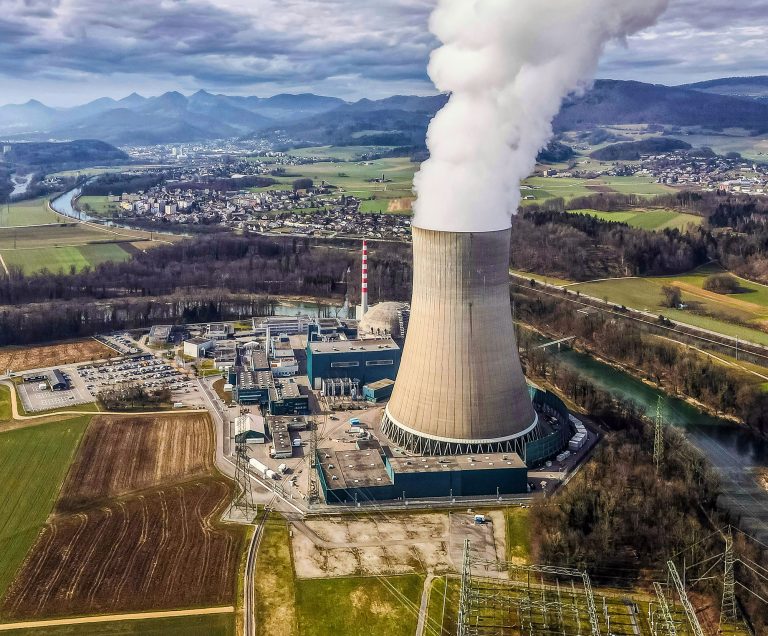
From Concept to Core: How ADDere Transforms Nuclear Reactor Components
Additive manufacturing has been gaining traction in the nuclear energy industry. The development and maintenance of nuclear reactors demand components that meet stringent safety standards
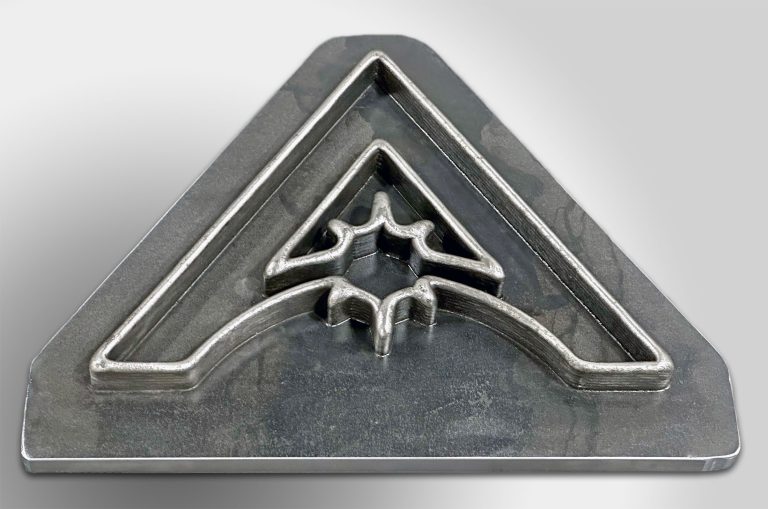
White Paper: The Impact of Additive Manufacturing on Cost, Efficiency & the Future
ADDere’s metal laser-wire additive process is a proven technology for producing complex large-scale metal parts for the defense and aerospace industries. With increasing interest in
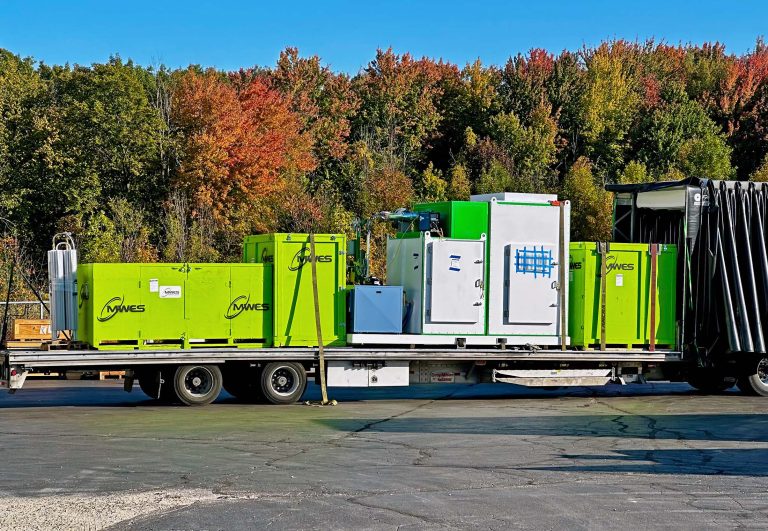
Cost-Benefit Analysis of ADDere’s Additive Manufacturing Process
ADDere’s metal additive manufacturing process has transformed the manufacturing landscape by enabling the production of complex parts with unprecedented precision. Additive manufacturing has evolved from