Inconel in the Aerospace Industry
Components Manufactured with Inconel
The aircraft manufacturing industry is turning to Inconel alloys during the build process for durability, corrosion resistance, rust resistant and strength. Inconel is used in the aerospace industry during applications where intensely high temperatures can be present, such as in jet engines. Under high heat, Inconel forms a protective oxide layer that makes it heat-resistant. Additionally, these alloys are highly resistant to pressure, oxidation and corrosion. The aerospace industry has many uses for Inconel due to these benefits, as well as its ability to be used for a number of mechanical purposes.
Here are some of the aerospace parts and components that are made with Inconel alloys:
- Gas turbine rotors, blades, and seals
- Afterburner parts
- Flame holders
- Heat exchangers
- Heat treating
- Heat shields
- Instrumentation components
- Combustion cans
- Aerospace liners
- Transition ducts
- Tubing, valves, piping, bolts, etc.
Properties and Aerospace Applications of Inconel
Inconel plays important role in protecting other components while encountering environments and situations with high pressures. These alloys are used in aircraft components that require a high degree of reliability under high pressures, such as heat shields, gas turbine blades and engine exhaust piping.
High-temperature resistance and the ability to stabilize itself over a wide range of temperatures are two features of Inconel that are highly sought-after in the aerospace industry. Aircraft parts that have to handle years of operation in high-temperature environments are ideal for Inconel. The jet engine and engine exhaust systems of aircraft greatly benefit when Inconel is incorporated into their systems. Inconel has a hardening feature that permits it to deal with high-heat situations better than materials such as steel and aluminum. Metal alloys are novel solutions to long-standing industrial problems such as the need for heat-resistant parts and materials.
Advantages of Inconel to Other Metals
Inconel is a superb choice for industrial and aerospace situations where the material is highly-resilient in the face of both high temperatures and chemical corrosion. This alloy is also able to withstand high-oxidation environments that would quickly degrade the integrity of most other metals and metal alloys. Here are four areas of applications where Inconel really stands out compared to other metals.
Heat Treating Applications
Inconel is capable of retaining an impressive amount of tensile strength even under intense levels of heat. Marlin Steel claims that Inconel 625 can retain 13.3 kilo-pounds per square inch of a load at 2,000°F. This makes it the material of choice for heat-treating applications, as it is capable of withstanding high temperatures better than stainless steel, titanium and other metals. This means that Inconel alloys would retain their heat-treated shapes much better than the majority of other metal alloys, including stainless steel alloys.
Adaptability in Changing Temperature Differences
There are times when it’s desirable to have a metal or metal alloy that handles environments with rapid changes between low and high temperatures. Inconel alloys tend to still possess their high oxidation resistance levels at both low and high temperatures. This means that the same Inconel part can be used in industrial processes with temperatures that shift from roughly cryogenic-level low temperatures to heat-treating-level high temperatures.
Resistance to Saltwater Exposure
Inconel has many uses in saltwater applications due to its high resistance to sodium chloride at a wide range of temperatures. Aerospace manufacturing uses Inconel in components that will become exposed to salt or in conditions that are near saltwater sources. While some stainless steel alloys are also highly resistant to saltwater, Inconel still has its advantages. In temperatures above 1,000°F, Inconel maintains its high oxidation resistance and has more utility than grade 316 of stainless steel at the same temperature.
Further, an article on AZO Materials brings to light that titanium can only retain its high resistance to saltwater corrosion up to about 500°F, making Inconel the superior choice to that alloy as well.
Jet Engine Construction
Inconel is a top pick for jet engine construction material because it can retain its high oxidation-resistant levels and tensile strength levels even under rapid and drastic temperature changes. These strengths apply even to the high-temperature combustion processes and the cooling systems used in the aircraft temperature control and regulation systems.
Inconel can easily be 3D printed
Using laser wire additive manufacturing processes like the ADDere system, large-scale Inconel parts can be printed to near-net shape quickly and easily.
ADDere’s additive manufacturing can streamline the development and production process of large-scale components made from Inconel. Contact us today and see if your manufacturing operations can benefit from ADDere’s additive manufacturing with Inconel.
Next Level Industrial-grade Laser Wire Additive Manufacturing
What's going on at ADDere
Latest Blog Posts
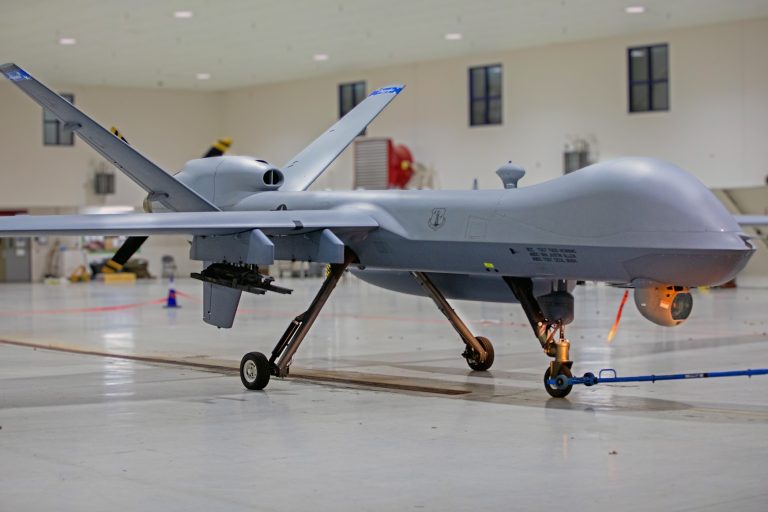
Harnessing ADDere’s Additive Manufacturing Process for Next-Generation Drones
Industrial applications of drones are soaring to new heights in 2025. From utilities and infrastructure inspection to agriculture and defense applications are industries that will
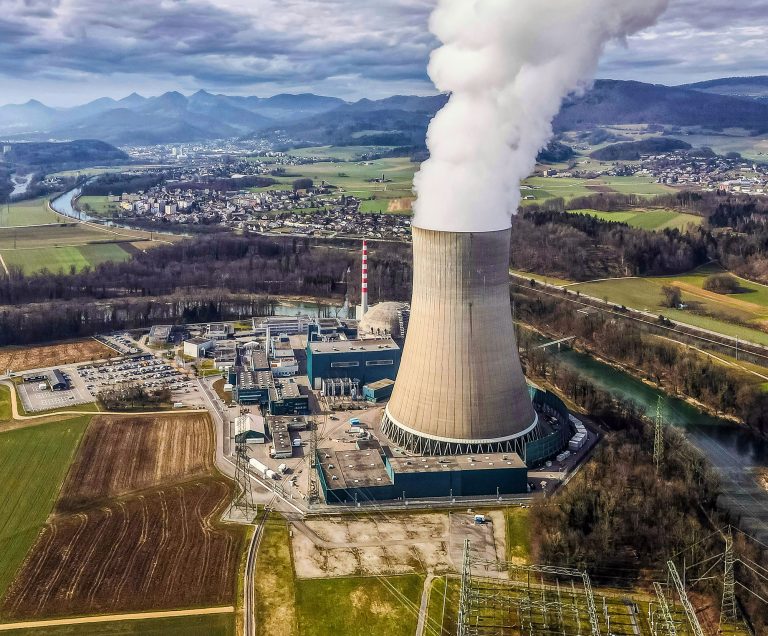
From Concept to Core: How ADDere Transforms Nuclear Reactor Components
Additive manufacturing has been gaining traction in the nuclear energy industry. The development and maintenance of nuclear reactors demand components that meet stringent safety standards
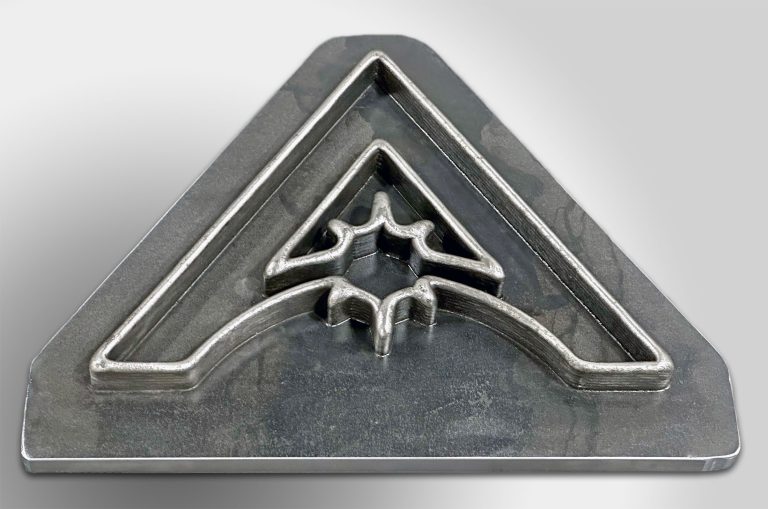
White Paper: The Impact of Additive Manufacturing on Cost, Efficiency & the Future
ADDere’s metal laser-wire additive process is a proven technology for producing complex large-scale metal parts for the defense and aerospace industries. With increasing interest in
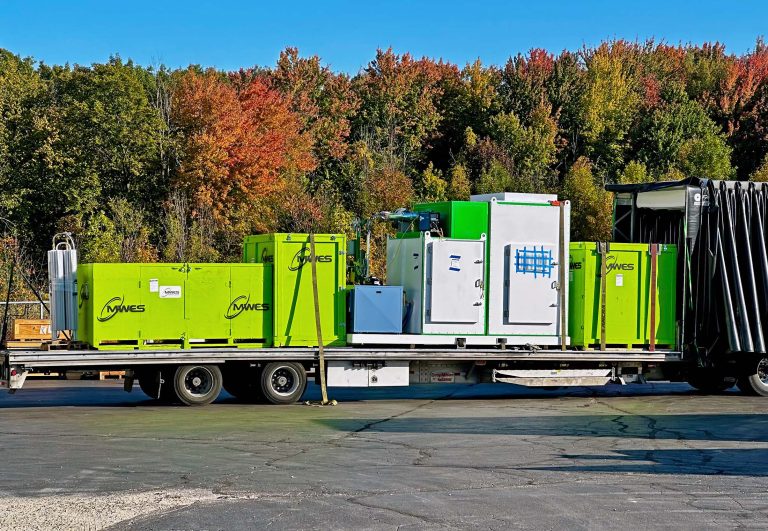
Cost-Benefit Analysis of ADDere’s Additive Manufacturing Process
ADDere’s metal additive manufacturing process has transformed the manufacturing landscape by enabling the production of complex parts with unprecedented precision. Additive manufacturing has evolved from
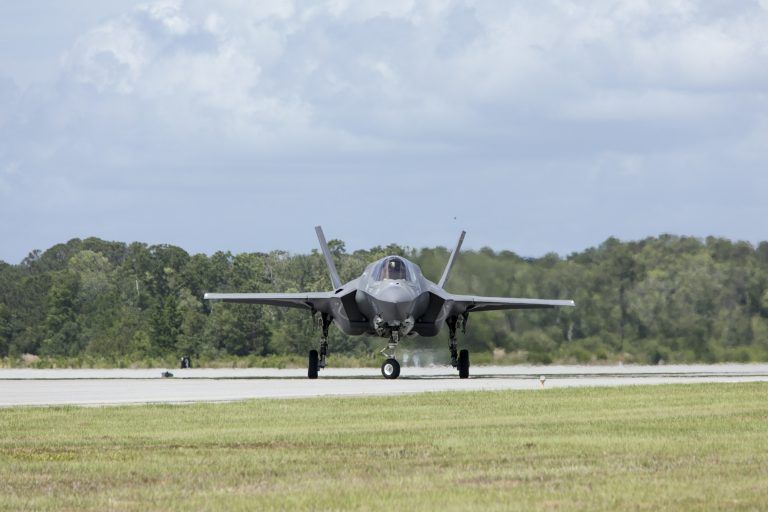
The Growing Role of Additive Manufacturing in Aerospace: Revolutionizing Metal Parts Production
The aerospace industry has always been at the forefront of technological innovation, constantly seeking ways to improve efficiency, performance and sustainability. From rapid prototyping to
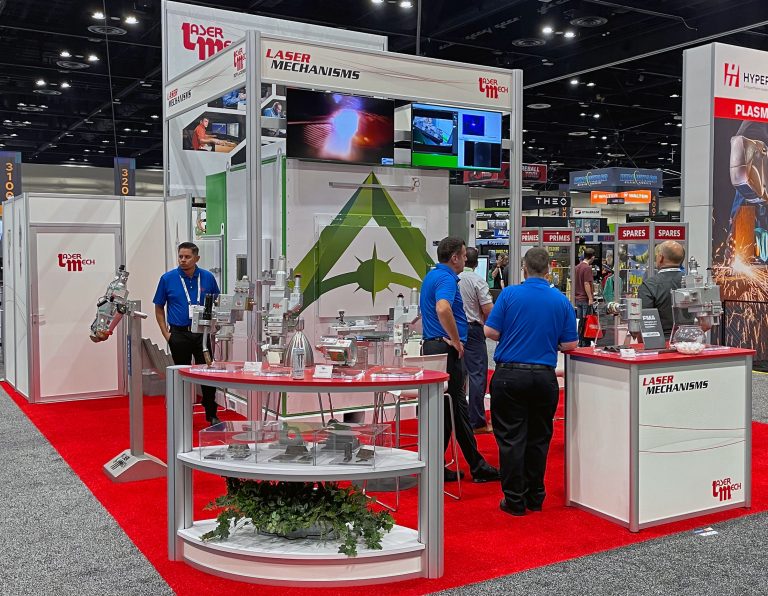
FABTECH 2024 Follow Up
Thank you to everyone who stopped by the Laser Mechanisms booth to see ADDere’s latest small format system at this year’s FABTECH in Orlando! The