ADDere’s additive manufacturing process represents a significant leap forward in producing industrial-scale parts. By utilizing a laser-wire additive system, ADDere can create large-scale, complex components from a variety of metal-based materials, including superalloys. This method allows for the creation of near-net-shaped parts with high precision and reduces material waste and production time. Industries ranging from aerospace to defense benefit from this technology, as it enables the production of large parts that were previously difficult to manufacture.
ADDere’s commitment to ITAR compliance ensures that sensitive information remains secure, making it a reliable partner for industries that require stringent data protection. The future of manufacturing is being reshaped by such innovative processes, which promise to enhance efficiency, reduce environmental impact and open up new possibilities in design and engineering.
3D Printing a Curved Pipe
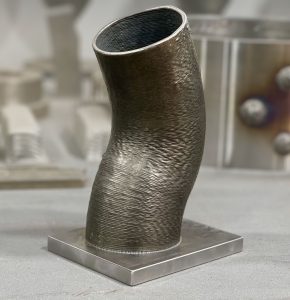
Below a timelapse video highlights the 3D print process of a 22 cm tall thin-walled curved pipe. The part was produced with stainless steel and the build time was about 3 hours. Using conventional casting processes, a part of this shape would require a unique cast to be constructed and molten steel poured into it. However, with ADDere’s additive manufacturing systems, a 3D model is all that is required to manufacture the part.
You can watch more videos featuring ADDere’s services on the Midwest Engineered Systems’ YouTube channel.
If you are looking at manufacturing low-run, custom or prototype parts then ADDere will provide your process with a solid return on investment when compared to conventional casting. Contact us today and we can guide you through our available options and how we can improve your manufacturing process.