Additive manufacturing has been gaining traction in the nuclear energy industry. The development and maintenance of nuclear reactors demand components that meet stringent safety standards and withstand extreme conditions. Many of these components are custom designs made from common metal alloys and superalloys that are difficult to otherwise traditionally machine or cast. ADDere’s additive manufacturing process is the ideal solution to meet those challenges.
3D printing metal alloy parts with ADDere offers many benefits and applications, including reduced manufacturing time, cost savings and the ability to produce complex geometries that are difficult or impossible with traditional methods. Additionally, ADDere can 3D print low-run, large-scale metal alloy parts on-demand while limiting the need for extensive parts warehousing.
Examples of Parts that can be 3D Printed
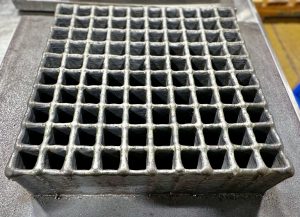
ADDere’s additive manufacturing process is ideal for producing any number of reactor parts.
- Control rod guide tubes and other intricate components within the reactor core
- Custom-designed piping, valves and fittings that are crucial for the reactor’s cooling and control systems
- Complex geometries of heat exchangers can be efficiently produced with ADDere
- Parts for pump assemblies that circulate coolant within the reactor system
- Housings and other parts for sensors and control systems
- Fuel debris filters that prevent unwanted materials from entering the fuel assembly
Why ADDere’s Metal 3D Printing is Ideal for Nuclear Reactor Maintenance
Precision in Complex Parts
One of the standout advantages of additive manufacturing is its ability to produce near-net-shaped metal parts with intricate geometries that traditional manufacturing methods struggle to achieve. Nuclear reactor components often require complex shapes and internal structures to optimize performance, enhancing cooling efficiency or reducing material stress. ADDere can create these complex parts layer by layer, allowing for previously unattainable designs.
Material Efficiency & Less Material Waste
Traditional manufacturing techniques often involve subtractive processes, removing excess material from a larger block to create the desired form. This can result in significant material waste, especially when working with expensive and critical materials like titanium or Inconel. Metal additive manufacturing, on the other hand, builds parts from the ground up, adding material only where it’s needed. This not only reduces waste but also lowers costs associated with raw materials.
Flexibility with Customized Parts
Nuclear reactors are highly specialized systems and their components often need to be tailored to specific requirements. ADDere offers unparalleled flexibility in design and customization. Engineers can quickly iterate on designs and produce custom parts without the need for costly and time-consuming retooling of machines. This adaptability is especially valuable for prototyping and producing small batches of components.
Shorter Lead Times
Time is of the essence in maintaining and upgrading nuclear reactors. Traditional manufacturing methods often involve lengthy lead times due to complex machining and assembly processes. ADDere’s additive manufacturing significantly reduces these lead times by streamlining production. Parts can be designed, printed and ready-to-go in a fraction of the time it would take using conventional methods, ensuring reactors are operational and efficient sooner.
On-Site Part Manufacturing
In the nuclear industry, the ability to produce spare parts on-site or near-site is a game changer. ADDere’s additive manufacturing systems can be installed on the same site as the nuclear reactor itself, reducing the need for extensive inventories and complex supply chains. This is particularly beneficial for aging reactors where certain parts may no longer be readily available from original suppliers.
What the Future Holds for Nuclear Reactors
The potential of ADDere’s metal additive manufacturing in the nuclear energy sector is vast and the industry has seen a recent resurgence. Ongoing research and development are exploring new material combinations and techniques to further enhance the capabilities of additive manufacturing. With advancements in quality control, post-processing and regulatory certifications, the adoption of ADDere for nuclear reactors can be expected to expand further.
Metal additive manufacturing is reshaping the landscape of nuclear reactor component production. Its ability to produce precise, complex, and customized parts, combined with material efficiency and reduced lead times, makes it an ideal solution for the nuclear industry. As ADDere pushes the boundaries of what’s possible, we are poised to play a critical role in ensuring the safe, efficient and sustainable operation of nuclear power plants for years to come.
Contact us today and we can print your low-run parts here at our ITAR compliant facility or we can quote you on one of our complete additive systems.