With most of our customers requiring the utmost secrecy, we really don’t have a lot of opportunities to show off our work. We do have clearance to show off this image.
What you’re looking at here is a close-up of a very large part (about a meter by meter by meter in volume) we’d made for proof of concept. It’s printed completely of stainless steel. The darker section is how the part looks after printing. The shiny section at the top is after a bit of machining. The thin band between them is the amount of material removed thus far in the process.
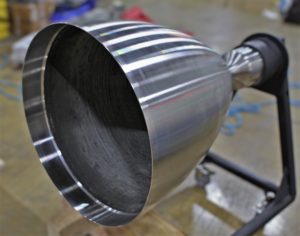
With about a 6mm path width, you can estimate that the shiny section isn’t anywhere near the width it was printed at – and that’s the genius of the ADDere laser wire additive process. Even though it prints wide paths, after secondary machining, intricate large components can be made at a fraction of the cost of digging out the shape from a solid block. And hawkeyed viewers can see that the ADDere process is unparalleled in the mitigation of inclusions and other quality issues found in conventional casting or other wire-based additive processes.
If you’d like to learn more about how ADDere can help reduce machining time on complex parts, contact us today!