ADDere’s metal additive manufacturing process has transformed the manufacturing landscape by enabling the production of complex parts with unprecedented precision. Additive manufacturing has evolved from a rapid prototyping solution to a fully-fledged manufacturing process that is revolutionizing how products are designed, produced and distributed. However, the adoption of metal additive manufacturing comes with its own set of costs and financial benefits that businesses must carefully consider.
The Cost Side of Metal Additive Manufacturing
The initial setup cost for a typical additive manufacturing system can be fairly substantial. The price tag for industrial-grade 3D printers, along with the necessary supporting equipment, energy consumption and materials, can run into hundreds of thousands of dollars or more depending on the scale of the system. Additionally, the relatively slow speed of 3D printing compared to traditional casting methods can lead to higher costs per unit for large production runs.
Maintenance & Operating Costs
While the initial investment in additive manufacturing equipment is high, ongoing maintenance and operating costs are relatively low. ADDere’s additive systems are designed for durability and thus require less frequent maintenance compared to traditional manufacturing equipment. Additionally, ADDere’s systems can be operated with a single operator, further reducing labor costs.
The Cost of Materials
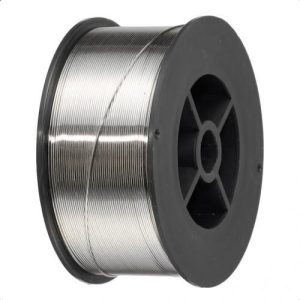
ADDere’s laser-wire additive process essentially uses off-the-shelf welding wire spools. The cost of welding wire ranges from a few hundred dollars a spool to over a thousand depending on the metal alloy. Metal powders, on the other hand, are generally far more expensive than traditional raw wire. The quality of the powder, particle size and specific alloy can significantly influence the cost. However, when compared to traditional subtractive manufacturing methods like CNC machining, which typically results in substantial material waste, additive manufacturing uses only the necessary amount of material.
The Benefit Angle
On the flip side, ADDere offers a plethora of benefits. The ability to create complex geometries that are impossible to achieve with conventional subtractive methods is perhaps the most significant advantage. This capability allows for the design and production of lightweight, yet strong components, particularly beneficial in industries such as aerospace and automotive.
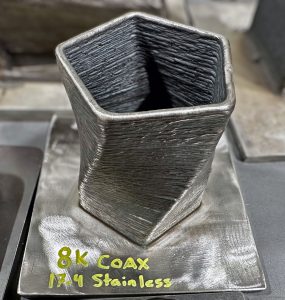
Build Unique Parts Efficiently
Part customization is another area where metal ADDere shines. It enables the production of parts tailored to specific applications without the need for expensive custom molds or tooling – all that is required is a standard 3D CAD drawing. This is especially advantageous for small batch production where traditional methods would be cost-prohibitive and a short lead time is required.
Produce Parts Quickly When Needed
ADDere revolutionizes supply chain and inventory management by enabling on-demand production. This is particularly beneficial for industries that require a wide variety of parts but in small quantities. On-demand production also minimizes the risk of obsolescence and reduces storage costs.
Breaking Even and Beyond
Studies suggest that additive manufacturing is most cost-effective for manufacturing small batches with centralized production. However, as automation increases and the technology matures, distributed production could become more financially viable. The key to cost-effectiveness lies in the value of the goods produced versus the costs incurred.
Material costs, which currently constitute a significant portion of the overall cost, are expected to decrease as the technology becomes more widespread and economies of scale come into play. This reduction in material costs, along with advancements in the speed and reliability of ADDere’s processes, could tip the scales in favor of broader adoption.
The Future Outlook
The future of ADDere and additive manufacturing in general is bright, with the potential for significant cost reductions, efficiency improvements and increased adoption. As the technology continues to evolve, we will likely see a shift in the manufacturing landscape, with ADDere’s additive manufacturing process becoming a more dominant force.
Businesses considering ADDere’s additive process and systems must conduct a thorough cost-benefit analysis, taking into account not only the direct costs and benefits but also the strategic advantages that the technology may offer in the long term. With careful planning and analysis, ADDere can be a powerful tool in your company’s manufacturing arsenal, offering flexibility, innovation, and a competitive edge.
If your business is considering reshoring your manufacturing and you want to stay ahead of the competition, then contact us today. Our additive specialists are here to guide you through the ins and outs of ADDeres’ additive manufacturing process and