The United States Navy has recognized the potential of additive manufacturing to improve its capabilities and readiness, especially in submarine and surface ship production, maintenance, and repair. The Navy has been investing in research and development of additive materials and processes, as well as exploring new applications and challenges of additive manufacturing in naval environments.
Submarine Production and Maintenance
The demand for new and modernized submarines is in high demand in the U.S. Navy. It plans to produce three submarines per year as well as upgrade and sustain the existing fleet. To meet these goals, the Navy needs to increase its manufacturing capacity and efficiency, as well as ensure the quality and reliability of the parts.
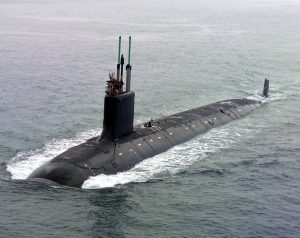
ADDere Additive Manufacturing can offer a solution to some of these challenges by enabling the production of complex and customized parts that are difficult or impossible to make by conventional methods. ADDere can create parts with internal channels, lattice structures or variable properties that can improve the performance, weight or stealth of the submarines. Additive manufacturing can also reduce the number of parts needed for assembly, simplifying the design and reducing the risk of failure.
The Navy has been working with industry partners to develop and qualify metal-alloy materials and processes for submarine applications. For instance, the Navy has collaborated with Huntington Ingalls Industries to produce a prototype propulsor for a Virginia-class submarine using additive. The propulsor is a large and complex part that consists of several components that are normally cast or forged separately and then welded together. By using 3D printed parts, the propulsor can be made as a single piece, reducing the manufacturing time and cost, as well as improving the quality and performance.
The Navy has also been exploring the use of additive manufacturing for on-board production and repair of submarine parts. This can reduce the dependence on external suppliers and logistics, as well as increase the availability and readiness of the fleet. The Navy has installed 3D printers on some submarines, namely the USS New Hampshire, to enable sailors to make spare parts on demand.
Surface Ship Production and Maintenance
The U.S. Naval surface ship construction sector is also facing similar challenges as the submarine sector, such as increasing demand, limited capacity and supply chain issues. The Navy plans to build more than 300 ships by 2030, including new classes of frigates, destroyers, amphibious ships and aircraft carriers. The Navy must also maintain and modernize its existing fleet of more than 290 ships.
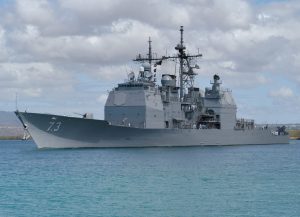
Additive manufacturing can provide benefits for surface ship production and maintenance by creating novel and optimized parts that can enhance the ships’ performance, survivability, or functionality. ADDere can create parts with complex geometries or multifunctional features that can improve the aerodynamics, hydrodynamics, or stealth of the ships. ADDere can also create parts with tailored properties or gradients that can improve the strength, stiffness, or durability of the ships.
The Navy has been collaborating with industry partners to develop and qualify metal-alloy materials and processes for surface ship applications. The Navy has partnered with Lockheed Martin to produce a titanium component for an antenna mast on a Freedom-class littoral combat ship using additive manufacturing. The component is a large and intricate part that would normally require multiple pieces to be machined and welded together. By using ADDere, the component can be made as a single piece, reducing the weight by 50%, increasing the strength by 30%, and reducing the fabrication time by 90%.
The Navy has also been experimenting with the use of additive manufacturing for on-board production and repair of surface ship parts. This can increase the agility and efficiency of the crews during missions in remote areas or hostile environments. In a pilot program, the Navy has installed 3D printers on warships to enable sailors to make spare parts or tools on demand. The Navy has also been testing new 3D printing processes for additive repair of surface ship components, such as laser cladding and wire arc additive manufacturing.
Future Opportunities
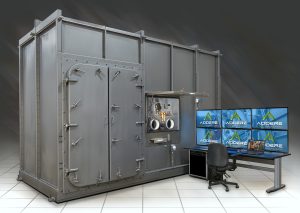
The Navy is committed to advancing the state-of-the-art of additive manufacturing for naval applications, as well as exploring new and novel approaches in developing and understanding metal alloy materials and processes. The Navy is also collaborating with other branches of the Department of Defense, academia, industry, and international partners to leverage the best practices and lessons learned from other domains and sectors.
ADDere Additive Manufacturing is a complete ITAR facility and has experience with defense department additive projects for the military. If your process is that of military, civilian or simply that of commercial applications then contact ADDere today and speak with us about your current operation.