In the dynamic world of manufacturing, ADDere’s laser-wire additive manufacturing process is emerging as a game-changer, offering a plethora of advantages over traditional manufacturing methods. With the ability to create complex geometries, produce large-scale customized components, fabricate multi-material parts, eliminate the need for assembly and minimize material waste, additive manufacturing is revolutionizing how we think about manufacturing. ADDere’s innovative approach revolutionizes how products are designed, prototyped and produced.
Design Freedom and Complexity
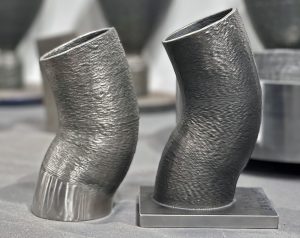
One of the most significant advantages of ADDere’s additive process is the unparalleled large-scale design freedom it provides. Traditional manufacturing methods are often constrained by the limitations of subtractive processes, which can stifle innovation. ADDere, on the other hand, allows for the creation of complex geometries that were previously deemed impossible or too costly to achieve. This includes intricate internal structures, such as lattice frameworks, which can optimize material usage and enhance part performance without compromising strength or integrity.
Rapid Prototyping and Rapid Iteration
The agility of ADDere in large-scale prototyping is unmatched. It significantly reduces the time required to develop prototypes, allowing for rapid iteration and refinement of designs. This accelerates the product development cycle, enabling companies to respond swiftly to market demands and technological advancements.
Material Efficiency and Waste Reduction
Laser-wire additive manufacturing is heralded for its material efficiency. Traditional manufacturing often involves subtractive processes that generate significant waste. In contrast, ADDere builds parts layer by layer, using only the necessary material, which results in minimal waste production. This not only conserves valuable resources but also reduces the environmental impact of manufacturing.
Custom Designed Unique Parts
The flexibility of ADDere extends to customization and the creation of unique parts. Each part can be tailored to specific requirements without the need for additional tooling or setup changes. This is particularly advantageous for industries where personalized products are in demand, such as medical implants and aerospace components.
Completely Toolless Production
Another notable benefit is the elimination of tooling in the production process. Traditional methods often require custom tools and molds, which can be expensive and time-consuming to produce. 3D printing circumvents this need, offering toolless production that can adapt quickly to design changes.
Structural Optimization and Lightweight Parts
Additive manufacturing facilitates structural optimization, enabling designers to create parts that are lighter yet stronger. By optimizing the distribution of material within a part, ADDere can produce components that achieve the desired performance with less material, leading to weight savings that are particularly beneficial in sectors like automotive and aerospace.
Distributed Manufacturing
The decentralized nature of additive manufacturing allows for distributed manufacturing, where parts can be produced closer to the point of use. This reduces the need for extensive inventory and logistics, cutting down on transportation costs and lead times.
Cost-Effectiveness and Scalability
While the initial investment in additive manufacturing technology can be significant, the long-term cost savings are considerable. ADDere’s large-scale additive systems can reduce inventory stock, decrease energy consumption, and are suitable for both high and low volumes of part production, making it a cost-effective solution for a wide range of applications. Additionally, its scalability is ideal for custom or limited-run productions, as well as for scaling up to larger volumes without the need for significant upfront investment in tooling.
Where does ADDere fit into all this?
ADDere’s additive manufacturing process is paving the way for a new era in industrial production. Its advantages over traditional manufacturing are clear: greater design freedom, rapid prototyping, material efficiency, customization, toolless production, structural optimization, distributed manufacturing and the ability to handle varying production volumes. The advantages of metal additive manufacturing are clear and impactful, offering a level of flexibility, efficiency and innovation that traditional manufacturing methods cannot match. As technology continues to advance, we can expect ADDere to play an increasingly vital role in the future of manufacturing across various industries.
If your manufacturing process requires an overhaul, then ADDere’s additive manufacturing systems may be the solution for your application. Contact us today and speak with one of our additive experts and discover if additive manufacturing is in your future.