Metal additive manufacturing is still a rather nascent industry. It’s unsurprising that there are many who are scratching their heads as to how this technology fits into their production processes – or if it should at all. This article is designed to mark out the general boundaries where a designer should begin to consider a metal additive or conventional process. We’ve built the above graphical representation of where the more common processes line up with metal additive technologies.
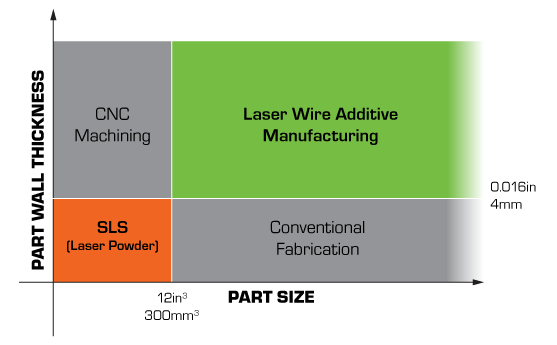
Starting at the lower left of the graph, the laser powder metal additive process, otherwise known as Selective Laser Sintering (SLS), has made significant inroads into modern manufacturing. The process can make intricate and nearly production-ready components – some of which could not be made with conventional processes. This is the most commonly known metal additive process.
Where SLS starts to lose its competitiveness is when a part exceeds a certain finished size or when that part leans more toward a carved solid mass. Typically, SLS printers have a build area of a cubic foot. While the process could be scaled indefinitely, both the printing time and the cost of the material used to print put heavy constraints on the large-scale feasibility.
When parts start to exceed the build area of a laser powder machine and still need to have fine details and thin mass, a combination of conventional fabrication processes should be explored. Laser cutting processes and advanced CNC fabrication can handle much larger parts while still offering the potential for similar tolerances.
For the parts that are more solid than complex, CNC machining is the direction to go. Starting from solid billet and carving features becomes more economical than waiting for the laser powder process to slowly build the thicker material. CNC production can also go well beyond the scales offered by typical SLS machines.
The same criteria that make CNC machining the champion over SLS, is where Laser Wire Additive Manufacturing (LWAM) begins to make more sense. More specifically, when a large metal part is needed that’s too large and high mass for SLS but would also require a substantial amount of time removing material on a CNC mill, LWAM is the direction to investigate.
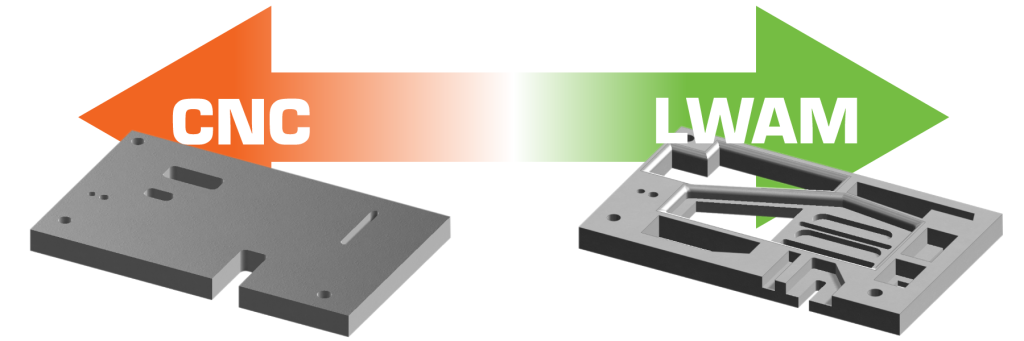
What LWAM can do is essentially 3D print a metal component at a casting grade of finish. Going with this process first can reduce CNC machining sometimes by more than 80% while saving waste material costs in the process. With LWAM, almost 97% of the material used in the process goes into the part. Where LWAM is not a good fit is where parts are small in scale and are extremely Complex.
While this is only a top-level look at how current metal additive methods interact with conventional processes, these generalizations should give a good foundation for indicating the proper processes to explore when selecting a technology to build components.
If you have more in-depth questions about the large-scale laser wire additive process, we can help lead you through the process and the benefits of integrating LWAM in your production process. Contact us today!