The metal additive world is awash in laser powder systems. They work great for highly detailed, precision parts – as long as they are on the small side. What if the part far exceeds the build volume of the usual Selective Laser Sintering (SLS) machines?
The good news is components can be additively manufactured using Directed Energy Deposition (DED) – like ADDere’s Laser Wire Additive process – at a much larger scale without incurring the time and costs needed to do it with powder processes, but it takes looking at the additive process a bit differently.
The big question is how big can DED systems print. Typical systems have build volumes that start around a meter cubed and then get larger from there. This volume is available for a number of metals beyond steel into more exotic metals like Inconel and even Titanium printing. This sort of scale puts the printing of components like trans-axle cases, frames and structural elements or large valves easily within the machine’s capabilities – and without the need to puzzle together a number of pieces to get there. These processes are adept at building high-mass parts, as well. They easily make the thicker sidewalls and other features when needed. Most systems in this group can put down material between 6 and 30kg per hour. That makes them perfect for large-size, high-mass parts.
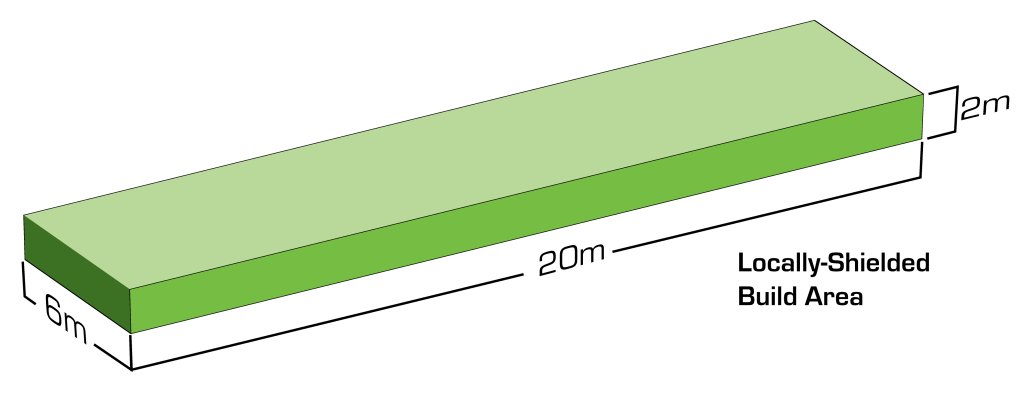
When switching to different production technologies, there will be tradeoffs: DED processes like ADDere’s have less resolution than SLS systems. There will need to be secondary finishing processes required to finish the DED printed part for assembly, although these processes will be the same as finishing conventional castings. Even with some machining processes after printing, these parts can still be ready to go faster than using SLS processes – and most times far less expensive (especially when nearly all the expensive material like Titanium goes into the part instead of the machine floor.) In fact, smart firms use the DED printed parts not only for testing components but testing the casting finishing processes at the same time, compounding the time savings using the printing process.
While laser powder has led the way for metal printing small parts, DED processes like ADDere’s Laser Wire Additive systems provide firms that deal in large-size, high-mass components with the benefits additive manufacturing provides, like a much faster development schedule and even flexibility in designing for specialized markets without having to engage time-consuming and expensive conventional processes for short runs.
Contact us today to learn how ADDere’s DED metal additive process can streamline your large component production process.