Metal additive processes have been working their way into manufacturing for some time, the bulk of that movement has been through laser powder systems. These technologies can make finely featured smaller-scale components. What happens when a firm needs a much larger scale part than what SLS systems usually make? It’s time to turn to a different additive process to achieve larger sizes in a more cost-effective manner, laser wire additive.
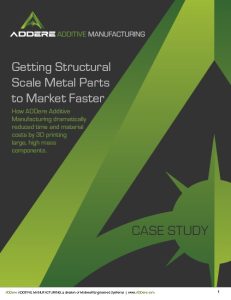
A 3D print’s success is balancing the shortcomings against the advantages and laser wire additive has a number of benefits. What would take an SLS system a month to print, LWAM can do in a few days. Its prints enjoy the least porosity and impurities of all additive processes while putting down massive amounts of material per hour. The cost for printing at such large scales and quality is typically found in a reduction in resolution. That can be overcome by properly integrating the additive process into existing production operations.
To help understand how laser wire additive best integrates into a prototype or low production run manufacturing operation, ADDere has put together a case study on how one company partnered with ADDere to build very large-scale metal additive components faster than their current processes alone.
Get the case study to learn more about how ADDere’s LWAM process can speed large-scale metal part manufacturing or contact us to learn more!