Why Print with ADDere
Bringing the power of Additive Manufacturing to large components and tough metals
When you have large components, it can be prohibitively expensive to adopt some measure of additive manufacturing. In most cases, it requires an investment in a complete system to prototype.
With ADDere Additive Manufacturing ITAR-compliant services, firms can prototype at a large scale and even run production quantities without the capital outlay or the relatively steep learning curve.
Advantages of Wire over Powder
While laser-wire Additive sometimes requires post-finish machining work, it allows for much larger prints than Selective Laser Sintering (SLS) printing methods. ADDere regularly prints up 2m x 1m x 1m in an envelope. That’s over three times the build area of most powder deposition systems on the market – and without the costs of printing at large scales in SLS machines where material waste on its own can make 3D printing prohibitively expensive.
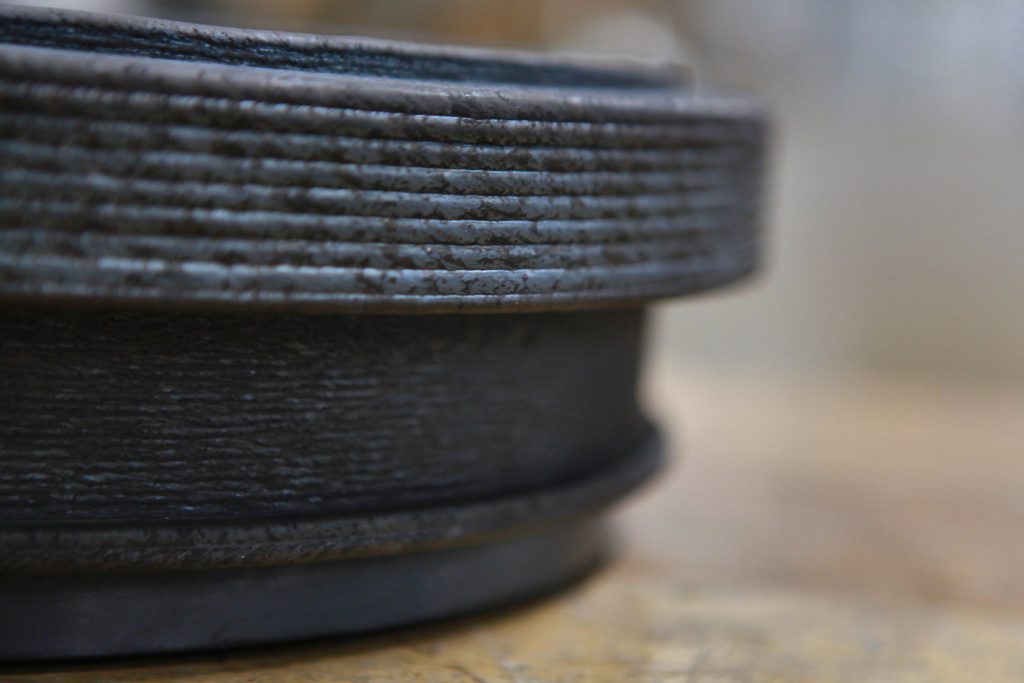
Faster than Casting
Some applications don’t require large runs, and the relatively time-consuming process of casting components usually becomes the best option. With ADDere additive manufacturing services, a firm can quickly print large-scale components without having to source small-run foundries or find vendors who can cast in exotic metals.
ADDere can print near net shape production-ready components that are comparable to sand casting – perfect for full-scale prototyping one-offs or small production runs. With its industry-leading closed-loop feedback system, ADDere can guarantee high-quality metallurgy across the entire product, side-stepping the costly process of testing pour quality.
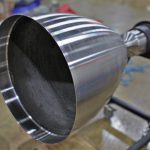
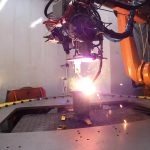
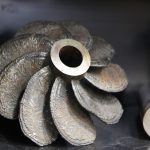
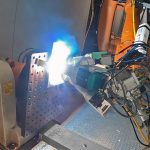
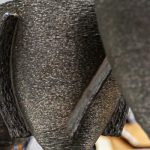
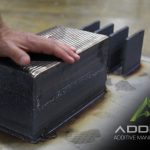
Less Wasteful than Machining
With ADDere Additive Manufacturing, large-scale metal 3D prints turn out to be far more economical as well, mainly due to a 1-2% material loss rate of the laser-wire additive process. That means 98-99% of the material needed is used in your product. No more having to bore out large quantities of exotic material like Inconel or Titanium with expensive bits. With ADDere, only finish machining would be required – save the expensive tooling for finish operations!
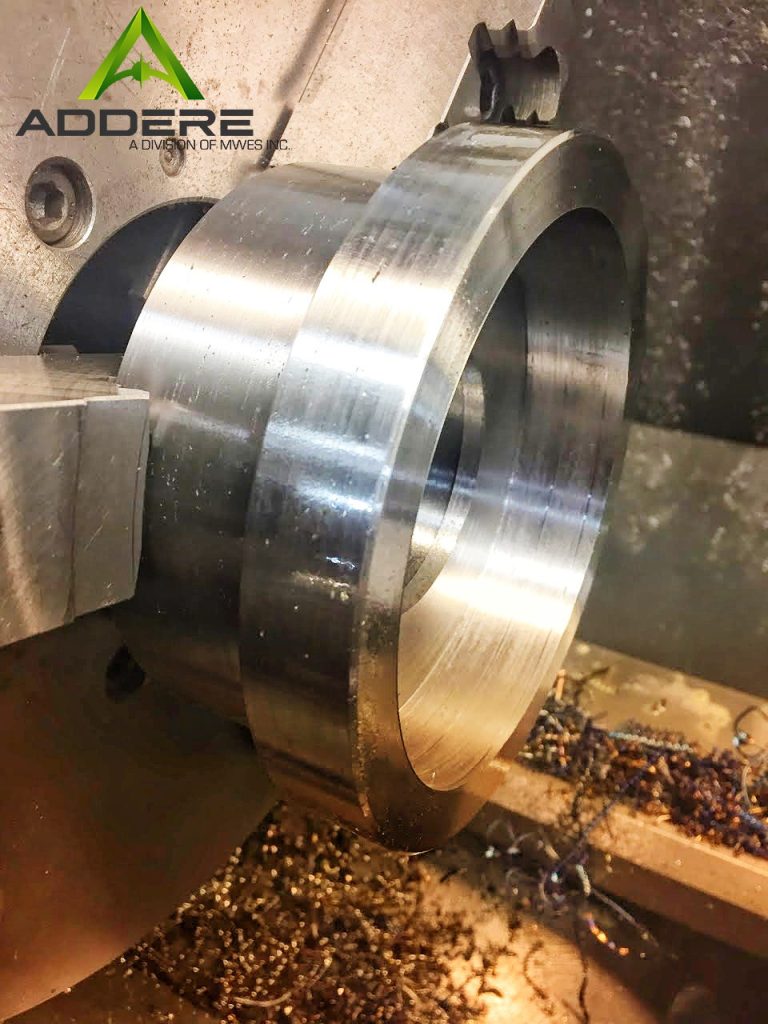
ADDere Print Services
Large components operate on their own economies from the high-volume parts made on laser-wire machines. Buying a large-scale additive manufacturing system without testing its abilities can feel like a gamble, especially when there are specialized requirements for the parts to be printed. Sometimes the number of components needed isn’t enough to rationalize the purchase of hardware needed to print the smaller runs. Many times it’s both.
In either case, ADDere understands the situation and provides metal printing as a service to manufacture these components on our machines. Whether to prove our system’s metal additive manufacturing abilities or to run parts without having to invest in 3D printing systems and training, ADDere can print your projects. Learn More…
do you want to learn more about ADDere's products and services?
Best-in-class Printing Performance
Sample Parts
Rocket Thrust Chamber
Deposition Rate: 4 lbs. per hour
Total Built Time: 20 hours
Material: Duplex Stainless Steel
Dimensions: 1 meter tall and 1 meter wide
System Used: ADDere Custom System
The final machined thrust chamber body has a sidewall thickness of 3mm with thicker walls in the combustion chamber.
Engine Exhaust/Intake Guarding
Deposition Rate: 4 lbs. per hour
Total Built Time: 40 hours
Material: Duplex Stainless Steel
Dimensions: 1 meter diameter
System Used: ADDere Custom System
A complex part made from stainless steel. This part was built as a single solid component.
Turbine Blade
Deposition Rate: 4.5 lbs. per hour
Total Built Time: 30 hours
Material: Duplex Stainless Steel
Dimensions: 1.8 meters tall
System Used: ADDere Custom System
The completed turbine blade has a hollow interior and a 5mm wide sidewall. It is 1800 layers tall with a height variant of 0.5mm.
Propeller
Deposition Rate: 3 lbs. per hour
Total Built Time: 4 hours
Material: Carbon Steel
Dimensions: Each blade is 25 cm long
System Used: ADDere Standard System
Thin-walled metal components are 3D printed directly onto an existing steel part in this case a piece of steel round bar.
Freeform Design
Deposition Rate: 4.5 lbs. per hour
Total Built Time: 20 hours
Material: Stainless Steel
Dimensions: Wingspan is 1.6 meters long
System Used: ADDere Custom System
A large demonstration part with a hollow 6mm wall thickness.
Wing Spar Cross-section
Deposition Rate: 6 lbs. per hour
Total Built Time: 1 hour
Material: Titanium Ti64
Dimensions: 50 cm long
System Used: ADDere Custom System
High-complexity 3D print in titanium. Cross-section aspects of 3D printing reduce construction times and make for a stronger overall part.
Thin Wall Curved Pipe
Deposition Rate: 6 lbs. per hour
Total Built Time: 3 hours
Material: Stainless Steet
Dimensions: 22 cm tall
System Used: ADDere Standard System
Custom-designed thin 4mm wall pipe that can be produced in different shapes and angles.
Fan Fins Assembly
Deposition Rate: 4 lbs. per hour
Total Built Time: 13 hours
Material: Stainless Steel
Dimensions: 1 meter diameter
System Used: ADDere Custom System
Custom-designed fan fin assembly with a hollow core.
Large Gear
Deposition Rate: 20 lbs. per hour
Total Built Time: 10 hours
Material: Stainless Steel
Dimensions: 1 meter diameter
System Used: ADDere Custom System
A custom-designed solid gear or sprocket made entirely from stainless steel.
Mold Die Form
Deposition Rate: 6 lbs. per hour
Total Built Time: 3 hours
Material: Carbon Steel
Dimensions: 25 cm diameter
System Used: ADDere Standard System
Rapidly produce custom plastic injection molding die forms with additive manufacturing.
From common metals to superalloys
Materials ADDere Prints
What's going on at ADDere
Latest Blog Posts
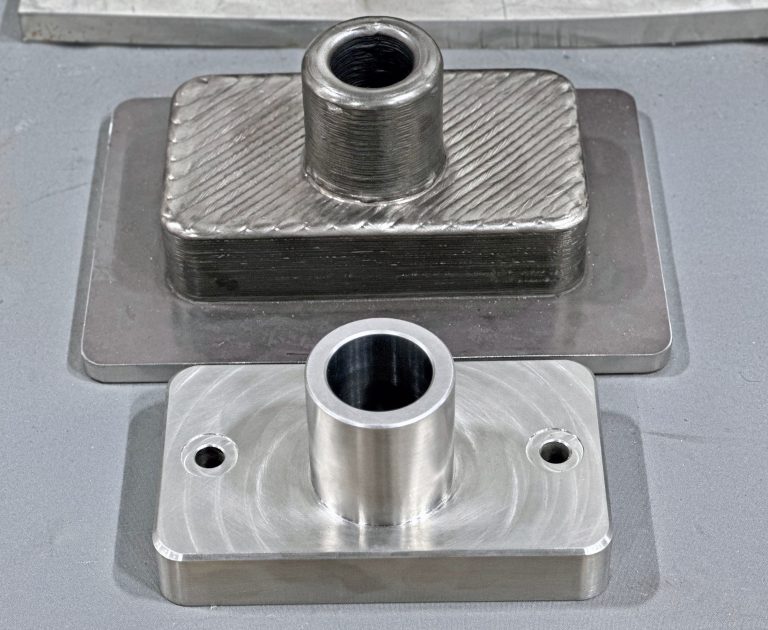
Are 3D Printed Metal Parts Produced with ADDere Strong?
ADDere’s additive manufacturing has revolutionized the production of strong metal-alloy parts, offering unprecedented flexibility and precision. One of the most exciting developments in this field
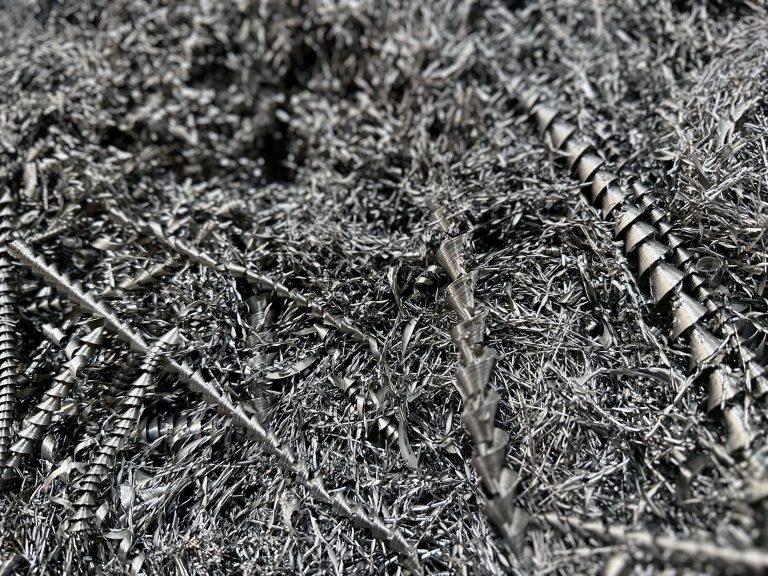
Mitigate Tariffs on Steel by Reshoring Your Manufacturing with ADDere
When it comes to large-scale metal parts manufacturing, ADDere can be a lifesaver for many businesses concerned with high import prices of steel. For decades,
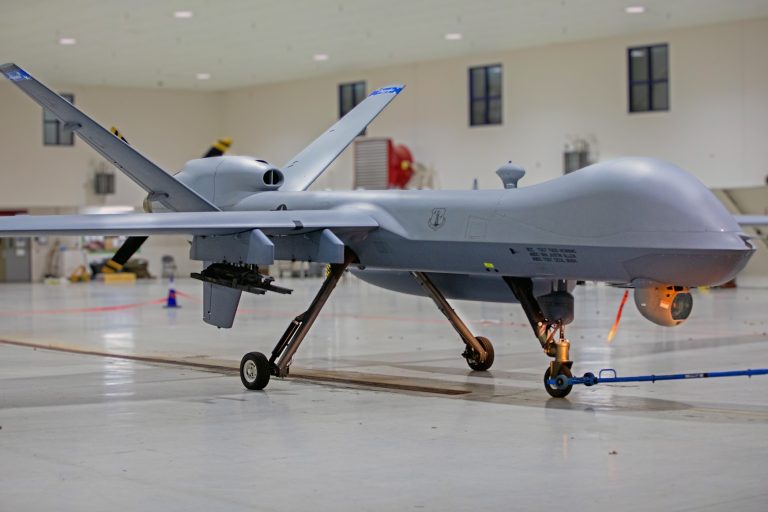
Harnessing ADDere’s Additive Manufacturing Process for Next-Generation Drones
Industrial applications of drones are soaring to new heights in 2025. From utilities and infrastructure inspection to agriculture and defense applications are industries that will
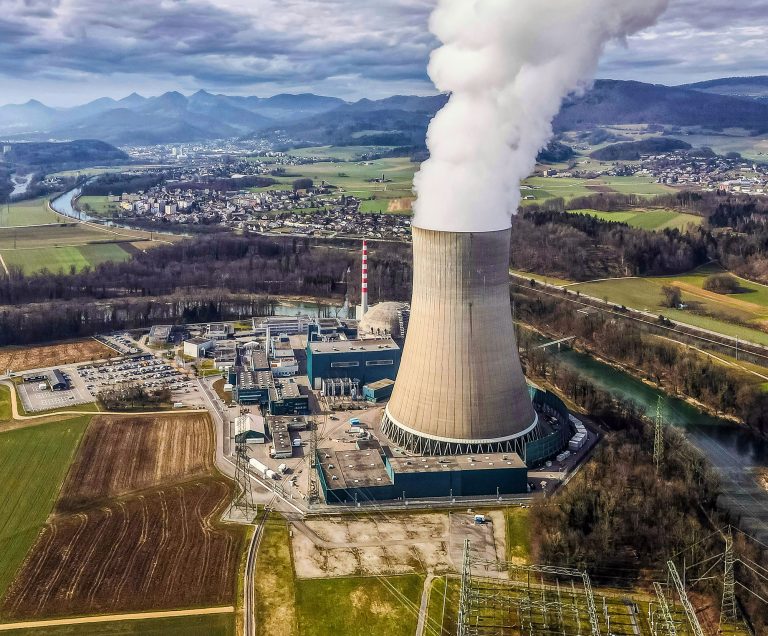
From Concept to Core: How ADDere Transforms Nuclear Reactor Components
Additive manufacturing has been gaining traction in the nuclear energy industry. The development and maintenance of nuclear reactors demand components that meet stringent safety standards
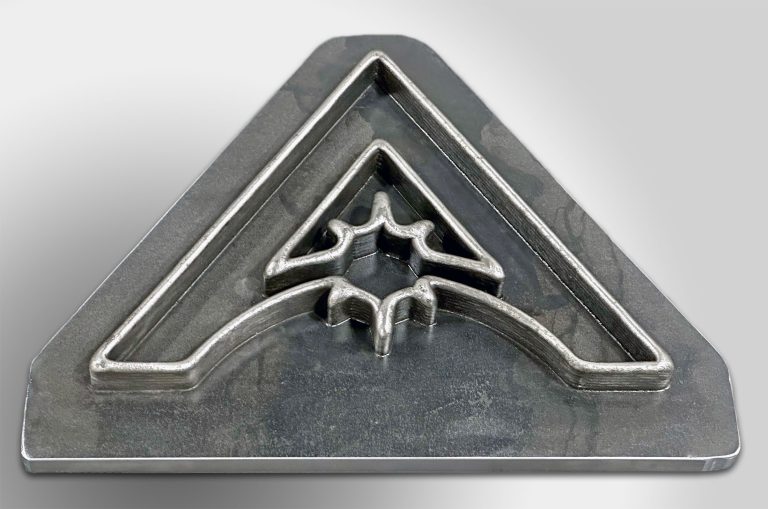
White Paper: The Impact of Additive Manufacturing on Cost, Efficiency & the Future
ADDere’s metal laser-wire additive process is a proven technology for producing complex large-scale metal parts for the defense and aerospace industries. With increasing interest in
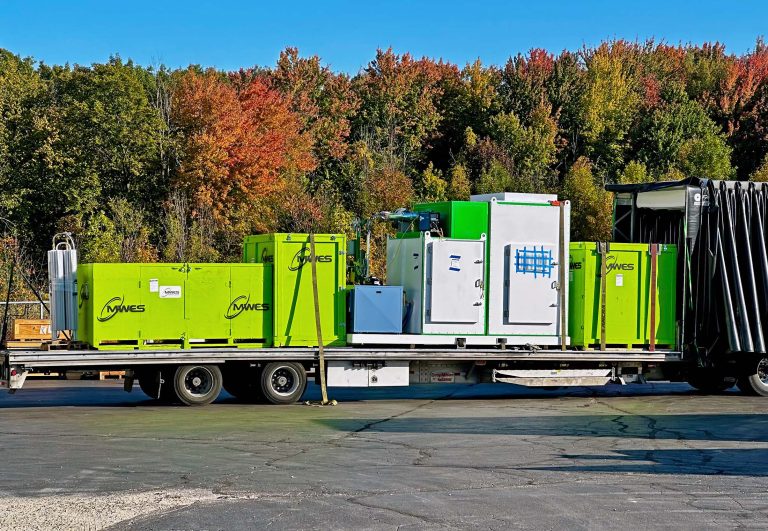
Cost-Benefit Analysis of ADDere’s Additive Manufacturing Process
ADDere’s metal additive manufacturing process has transformed the manufacturing landscape by enabling the production of complex parts with unprecedented precision. Additive manufacturing has evolved from