Hastelloy
A metal for highly corrosive environments
Hastelloy is an ideal material for highly corrosive environments which makes ADDere’s large-scale additive systems ideal for manufacturing complex parts. Hastelloy is a nickel metal that has been alloyed to increase corrosion resistance. This is primarily done through the addition of molybdenum and chromium. There are many grades of Hastelloy, with each grade having a different chemical makeup to be optimized for a specific set of properties. Because of Hastelloy’s qualities, it performs better in severely corrosive environments than other specialty metal products. The addition of molybdenum also increases general workability. Hastelloy alloys are also ductile and are easily fabricated and formed.
Typical Applications for Hastelloy
Given Hastelloy is designed to have outstanding corrosion resistance, it makes a great choice for any moderate to severely corrosive environments where product lifetime is important. With its resistance to oxidizing agents and acids, parts made from Hastelloy are commonly used in pipes and valves in the chemical and petrochemical industries. It is also used in reactor vessels in the chemical and nuclear industries. Hastelloy is also commonly used in harsh environments such as paper and pulp production and waste treatment.
ADDere’s additive manufacturing can streamline the development and production process of large-scale components made from Hastelloy. Contact us today and see if your manufacturing operations can benefit from ADDere’s additive manufacturing with Hastelloy.
do you want to learn more about ADDere's products and services?
What's going on at ADDere
Latest Blog Posts
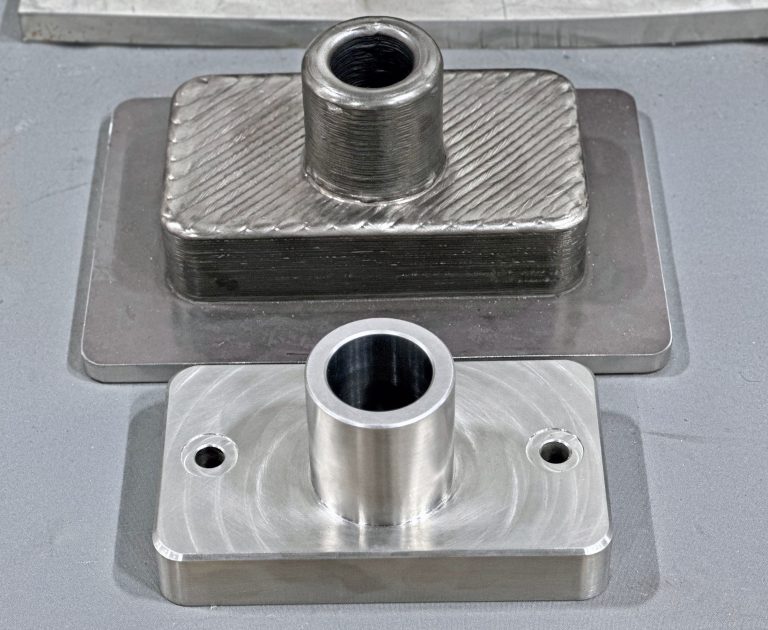
Are 3D Printed Metal Parts Produced with ADDere Strong?
ADDere’s additive manufacturing has revolutionized the production of strong metal-alloy parts, offering unprecedented flexibility and precision. One of the most exciting developments in this field
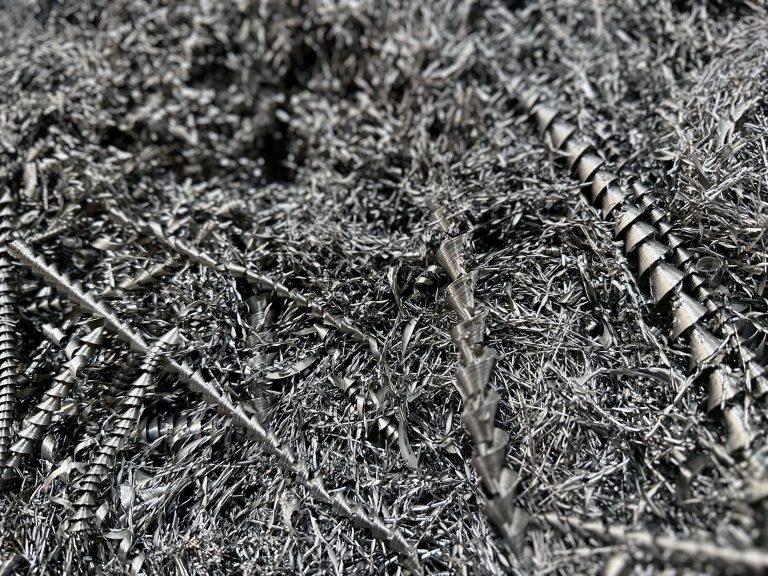
Mitigate Tariffs on Steel by Reshoring Your Manufacturing with ADDere
When it comes to large-scale metal parts manufacturing, ADDere can be a lifesaver for many businesses concerned with high import prices of steel. For decades,
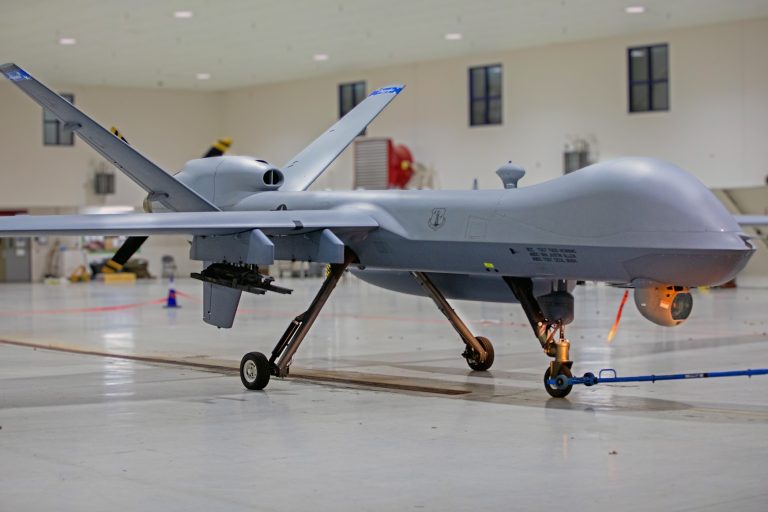
Harnessing ADDere’s Additive Manufacturing Process for Next-Generation Drones
Industrial applications of drones are soaring to new heights in 2025. From utilities and infrastructure inspection to agriculture and defense applications are industries that will
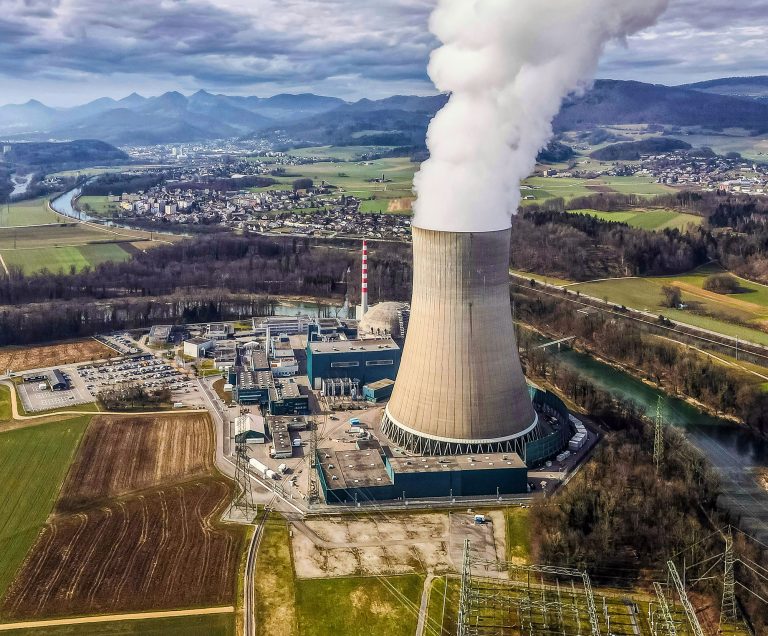
From Concept to Core: How ADDere Transforms Nuclear Reactor Components
Additive manufacturing has been gaining traction in the nuclear energy industry. The development and maintenance of nuclear reactors demand components that meet stringent safety standards
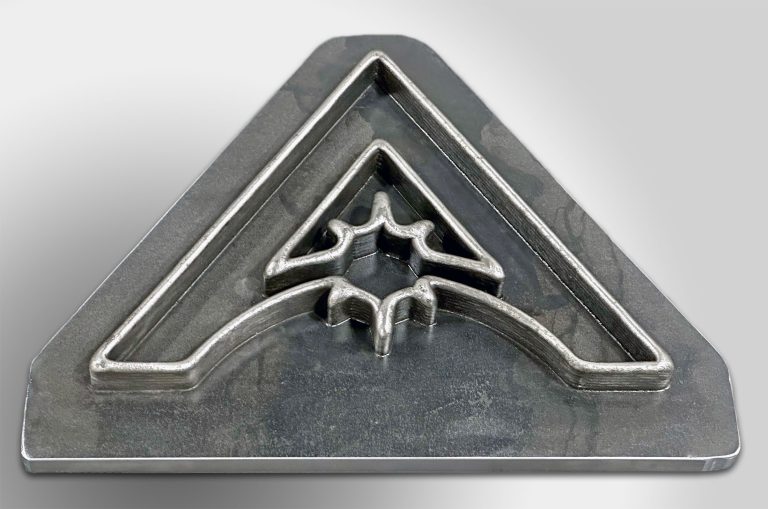
White Paper: The Impact of Additive Manufacturing on Cost, Efficiency & the Future
ADDere’s metal laser-wire additive process is a proven technology for producing complex large-scale metal parts for the defense and aerospace industries. With increasing interest in
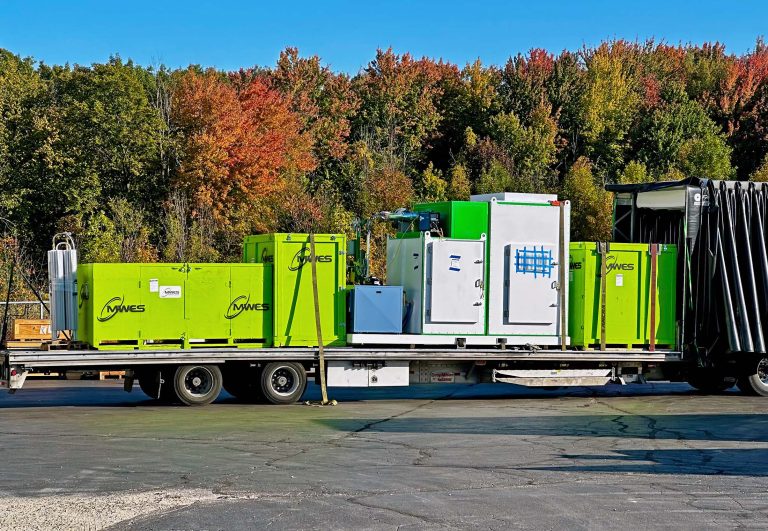
Cost-Benefit Analysis of ADDere’s Additive Manufacturing Process
ADDere’s metal additive manufacturing process has transformed the manufacturing landscape by enabling the production of complex parts with unprecedented precision. Additive manufacturing has evolved from