Titanium in the Aircraft Manufacturing Industry
Manufacturing aircraft with Titanium
The aerospace industry is one of the leading users of Titanium, and the development of aircraft components from the element has grown tremendously after the discovery of its capability. The technologies surrounding the development of airplanes have only increased the demand for Titanium. Aside from the commercial aerospace industry, the military also has driven demand for the element. The United States, for example, is one of the countries with the largest demand for Titanium for its commercial and military purposes. The titanium additive manufacturing industry is booming as a large number of clients are looking for more innovative and cost-effective airplane parts made of Titanium.
The two largest commercial airplane manufacturers in the world today – Boeing and Airbus – have a huge demand for the element. Titanium components are being increasingly employed in aircraft from Boeing, Airbus and other firms around the world. Without using Titanium as the base metal for their airplanes, performance losses from increased weights would reduce efficiencies and harm flight characteristics. With smaller production runs and more specialized components of greater complexity, the need for 3D printing titanium will rise in the coming years.
The amount of Titanium used by commercial aerospace manufacturing projects is dwarfed in comparison to the demand from the defense industry. Aircraft manufacturers supplying the military with advanced metal components are saying that an increasing amount of Titanium is required to build the airplanes that the military orders, including the F-22 Raptor, F-35 Lightning II, C-17 Globemaster and the UH-60 Black Hawk Helicopter. As a result, the United States and other militaries are conducting partnerships and research programs to reduce the cost of titanium production including additive metal manufacturing processes like the ADDere system. With 3D printing, the possibility of increasing the utility of Titanium increases as the limitations and cost of production from conventional processes are vastly mitigated.
Why build Titanium components
Many experts believe that aside from using the element to build today’s airplanes, engineers of the future will find increasing methods for using the material to extend the capabilities of aircraft in the future. With the speed of material science developments, the idea of hypersonic flight becomes more and more of a possibility and using Titanium will unlock the possibility to travel at those speeds. But for now, the experts are still looking for endless possibilities of using the element in extending today’s airplane operational efficiency.
The outlook is bright for manufacturing aerospace components in various titanium alloys as newer manufacturing processes like ADDere’s laser wire additive manufacturing systems begin to take center stage in the low run and prototyping aspects of titanium component production. The metal 3D printing industry is positioned to allow for reducing today’s production constraints as well as being able to fully utilize Titanium’s unique properties in a more cost-effective manner.
ADDere’s additive manufacturing can streamline the development and production process of large-scale components made from titanium. Contact us today and see if your manufacturing operations can benefit from ADDere’s additive manufacturing with titanium.
do you want to learn more about ADDere's products and services?
What's going on at ADDere
Latest Blog Posts
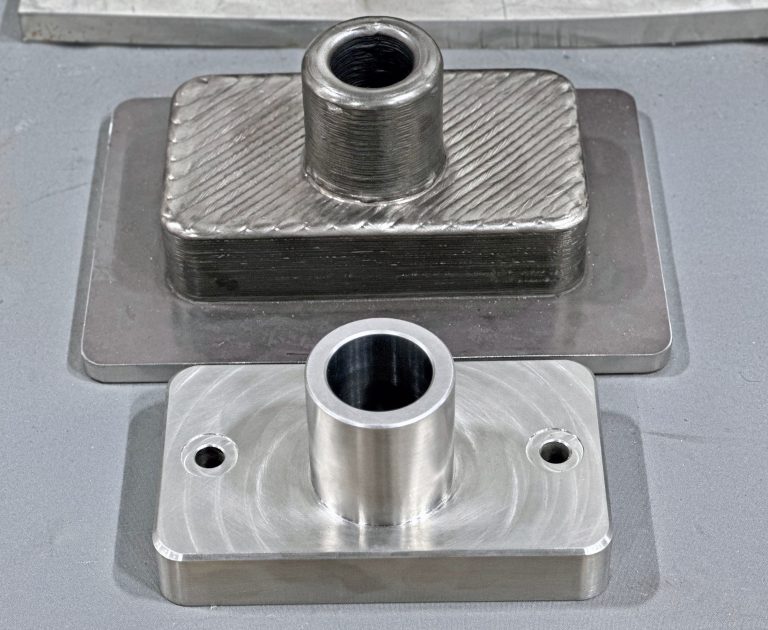
Are 3D Printed Metal Parts Produced with ADDere Strong?
ADDere’s additive manufacturing has revolutionized the production of strong metal-alloy parts, offering unprecedented flexibility and precision. One of the most exciting developments in this field
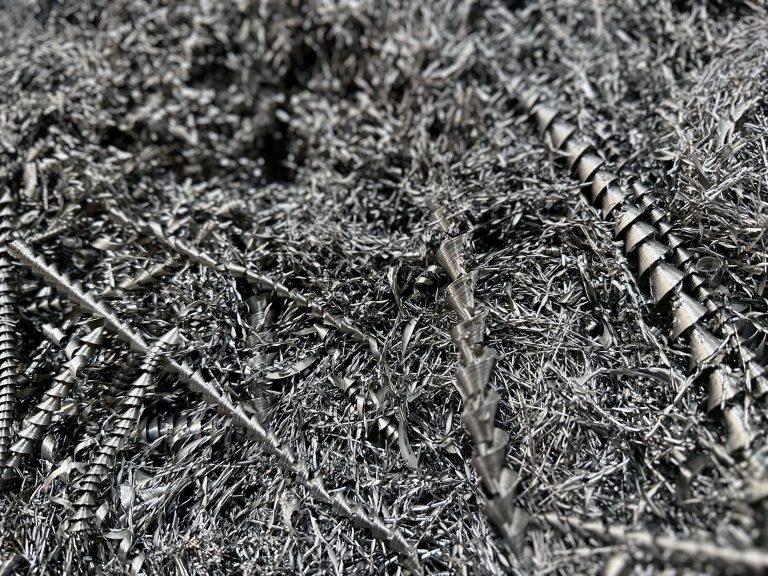
Mitigate Tariffs on Steel by Reshoring Your Manufacturing with ADDere
When it comes to large-scale metal parts manufacturing, ADDere can be a lifesaver for many businesses concerned with high import prices of steel. For decades,
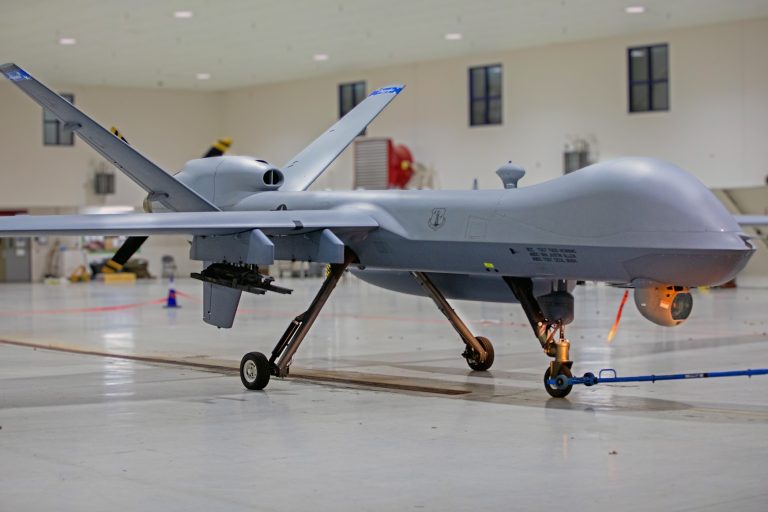
Harnessing ADDere’s Additive Manufacturing Process for Next-Generation Drones
Industrial applications of drones are soaring to new heights in 2025. From utilities and infrastructure inspection to agriculture and defense applications are industries that will
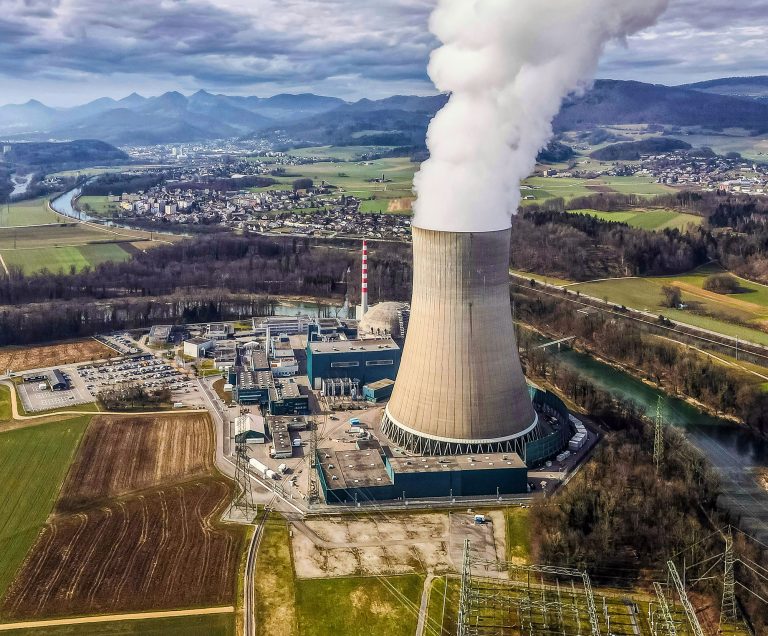
From Concept to Core: How ADDere Transforms Nuclear Reactor Components
Additive manufacturing has been gaining traction in the nuclear energy industry. The development and maintenance of nuclear reactors demand components that meet stringent safety standards
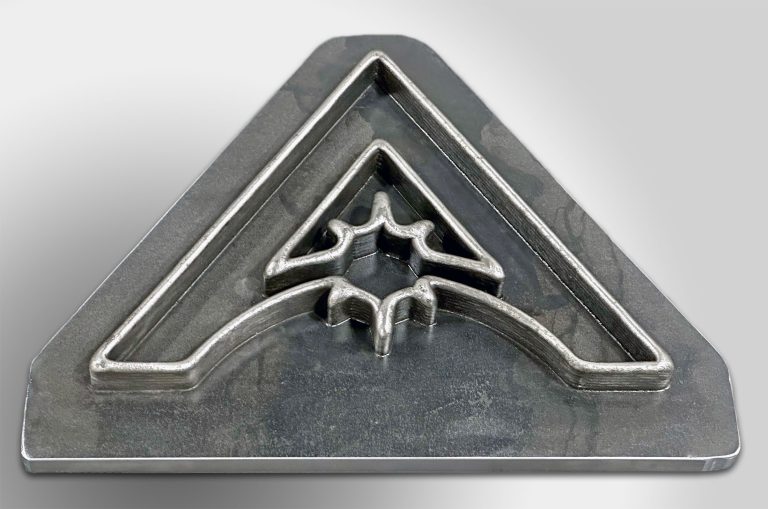
White Paper: The Impact of Additive Manufacturing on Cost, Efficiency & the Future
ADDere’s metal laser-wire additive process is a proven technology for producing complex large-scale metal parts for the defense and aerospace industries. With increasing interest in
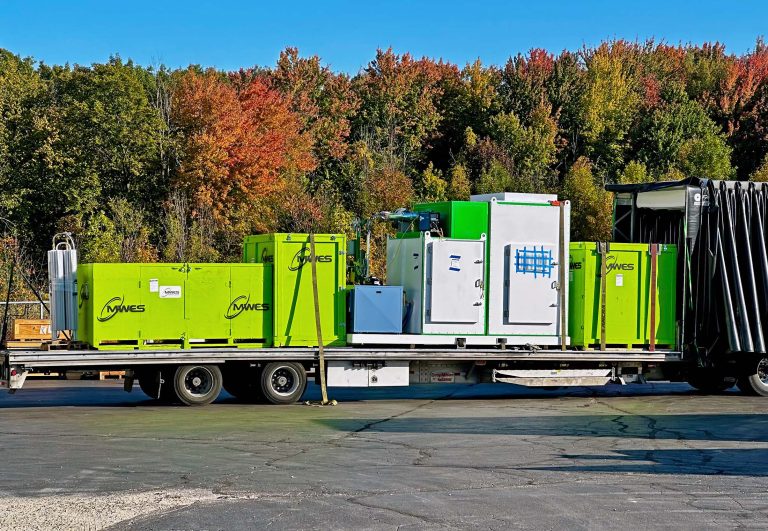
Cost-Benefit Analysis of ADDere’s Additive Manufacturing Process
ADDere’s metal additive manufacturing process has transformed the manufacturing landscape by enabling the production of complex parts with unprecedented precision. Additive manufacturing has evolved from