Piping & Ducts
Let ADDere print your
Piping, Tubing & ductwork
Piping, tubing and duct networks have the potential to be extremely complex, made from hundreds to thousands of differing parts. Custom unique fittings and connectors are commonplace in such complex piping and ductwork, and fabricating custom one-off parts can be cost-prohibited when done with casting. In addition, piping and ducts can potentially carry highly corrosive materials requiring them to be made from an alloy that is both durable and corrosion-resistant. ADDere Additive Manufacturing can manufacture custom one-off piping parts quickly and cost-effectively from any number of metal-based alloys, including superalloys.
Some of the benefits of using additive manufacturing for piping and ducts are:
- Improved fluid flow – ADDere can create smooth internal surfaces, reducing friction and turbulence in the fluid flow. This can improve the efficiency and reliability of the piping and ducts, as well as reduce noise and vibration.
- Enhanced thermal management – ADDere can create hollow structures with internal channels for cooling or heating fluids. This can improve the thermal performance of the piping and ducts, as well as reduce the risk of thermal stress and fatigue.
- Increased durability – ADDere can use high-performance superalloy metals that can withstand high temperatures, pressures, and corrosive environments. This can increase the lifespan and safety of the piping and ducts, as well as reduce maintenance costs.
Custom-designed parts made with additive manufacturing are becoming more popular in various industries, such as aerospace, automotive and petrochemical. 3D printed parts allow for greater design flexibility, reduced material waste and lower production costs. Piping and ducts made with additive manufacturing can have complex shapes, optimized performance and customized features that are not possible with traditional methods.
The ADDere laser-wire additive manufacturing system specializes in producing 3D printed large-scale, near-net-shape parts in a variety of metals including Titanium, Inconel, Stainless Steel and other superalloys, as well as most Ferrous-based metals. Contact us today if your business is interested in additive manufacturing.
ADDere Print Details
Deposition Rate: 6 lbs. per hour
Total Built Time: 3 hours
Material: Stainless Steel
Dimensions: 22 cm tall w/ 4 mm walls
System Used: ADDere Standard System
do you want to learn more about ADDere's products and services?
What's going on at ADDere
Latest Blog Posts
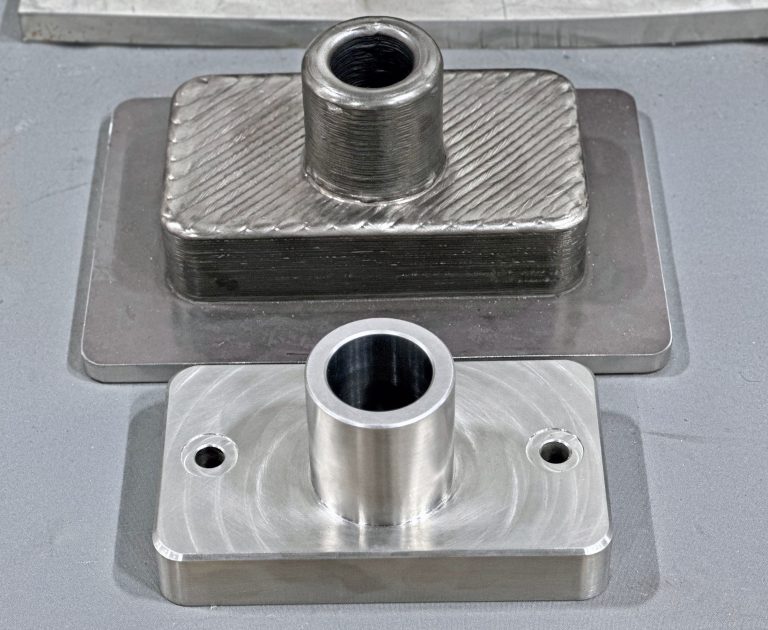
Are 3D Printed Metal Parts Produced with ADDere Strong?
ADDere’s additive manufacturing has revolutionized the production of strong metal-alloy parts, offering unprecedented flexibility and precision. One of the most exciting developments in this field
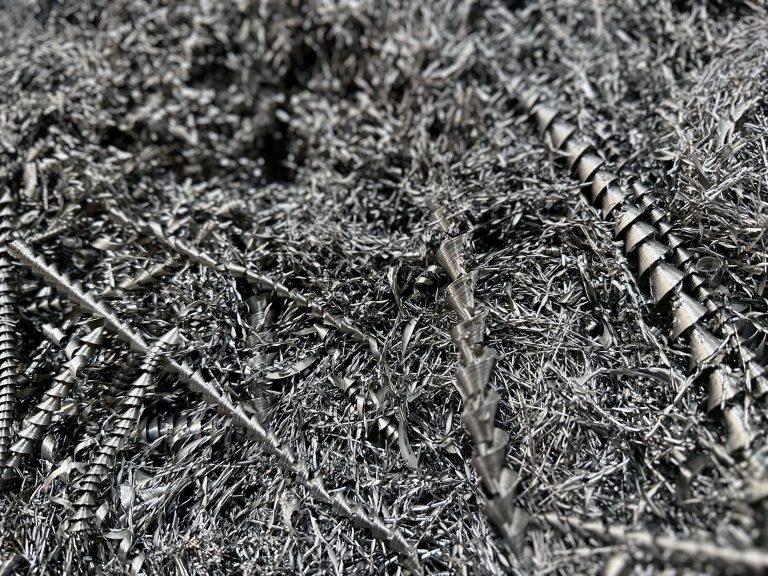
Mitigate Tariffs on Steel by Reshoring Your Manufacturing with ADDere
When it comes to large-scale metal parts manufacturing, ADDere can be a lifesaver for many businesses concerned with high import prices of steel. For decades,
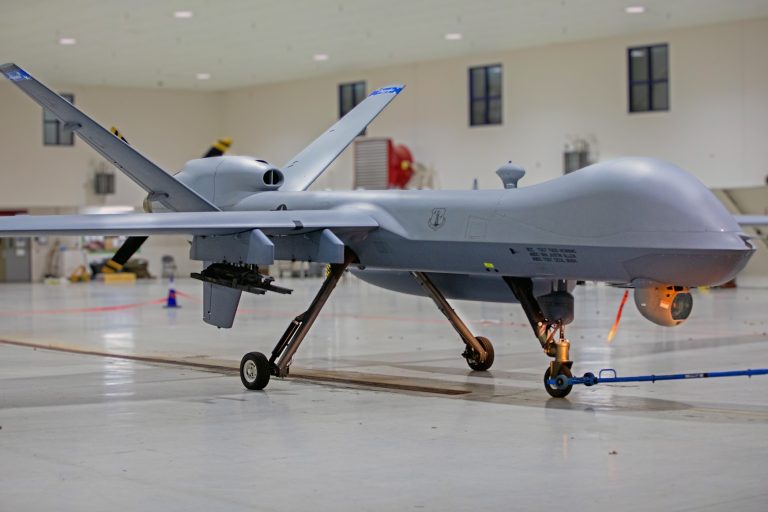
Harnessing ADDere’s Additive Manufacturing Process for Next-Generation Drones
Industrial applications of drones are soaring to new heights in 2025. From utilities and infrastructure inspection to agriculture and defense applications are industries that will
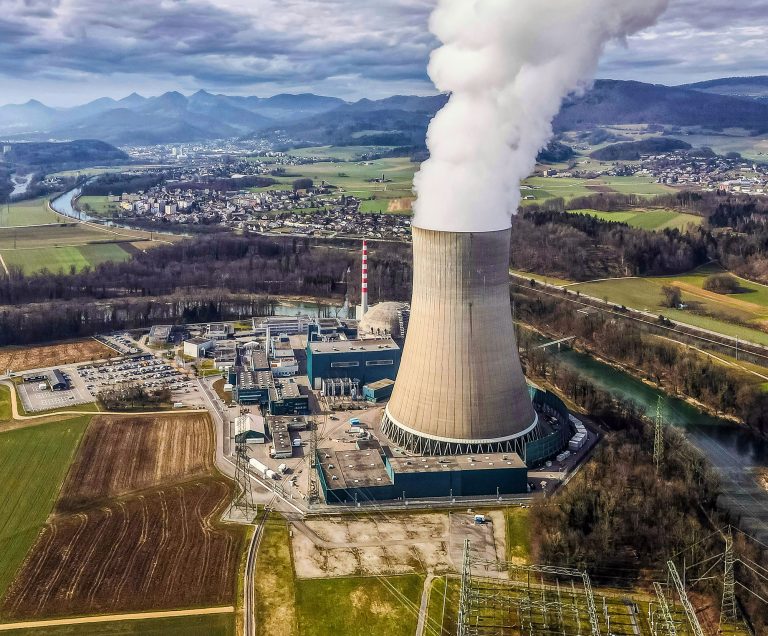
From Concept to Core: How ADDere Transforms Nuclear Reactor Components
Additive manufacturing has been gaining traction in the nuclear energy industry. The development and maintenance of nuclear reactors demand components that meet stringent safety standards
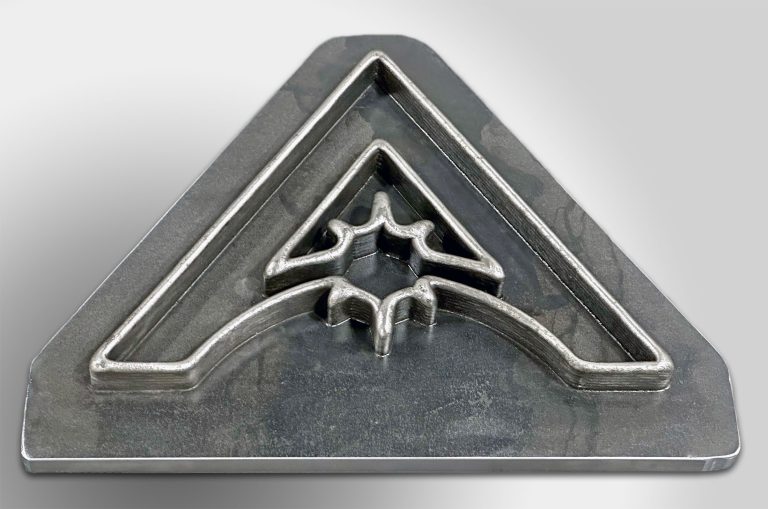
White Paper: The Impact of Additive Manufacturing on Cost, Efficiency & the Future
ADDere’s metal laser-wire additive process is a proven technology for producing complex large-scale metal parts for the defense and aerospace industries. With increasing interest in
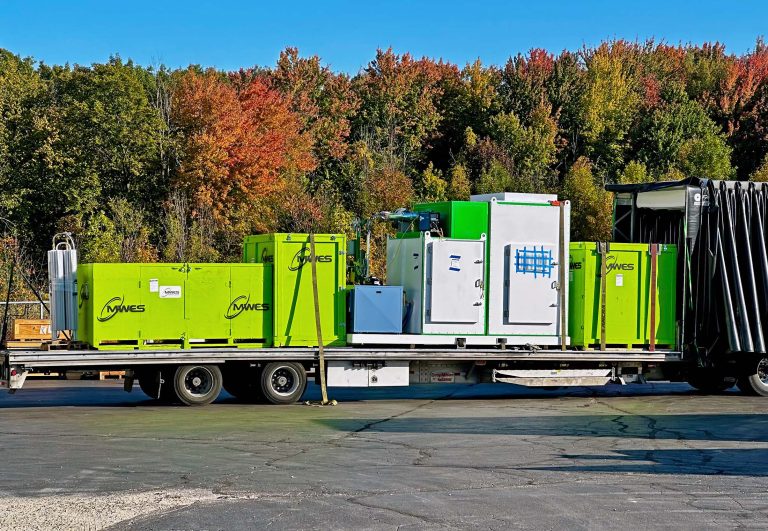
Cost-Benefit Analysis of ADDere’s Additive Manufacturing Process
ADDere’s metal additive manufacturing process has transformed the manufacturing landscape by enabling the production of complex parts with unprecedented precision. Additive manufacturing has evolved from