ADDere’s additive manufacturing has revolutionized the production of strong metal-alloy parts, offering unprecedented flexibility and precision. One of the most exciting developments in this field is the use of Laser Wire Additive Manufacturing (LWAM) to produce metal parts. LWAM facilitates the creation of dense, homogeneous parts that show uniformity throughout their structure.
A standout feature of ADDere’s LWAM-produced metal parts is their exceptional strength and durability. The laser-based melting process creates a highly controlled environment, leading to parts with optimal microstructure and fewer defects. This results in parts with superior mechanical properties, including high tensile strength, fatigue resistance and hardness. This addresses common issues found in traditional manufacturing methods, such as porosity and weak points, ensuring that the final product is robust and reliable. But how strong are these 3D printed metal parts compared to those made using traditional methods?
Understanding ADDere’s LWAM
Laser Wire Additive Manufacturing is an innovative process that involves using a laser to melt metal wire, which is then precisely deposited layer by layer to create metal parts. This method offers high precision and the ability to produce complex geometries, making it an ideal choice for industries that require robust and reliable components.
Unparalleled Strength and Durability
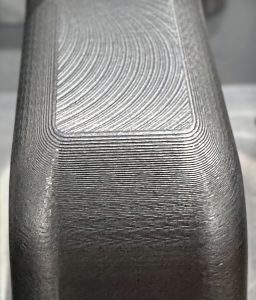
One of the most significant advantages of LWAM-produced metal parts is their exceptional strength and durability. The laser-based melting process ensures a highly controlled environment, resulting in parts with optimal microstructure and minimal defects.
The ability to control the microstructure during the printing process ensures optimal density and eliminates common defects found in traditional methods, such as porosity and grain boundaries. This meticulous method leads to components with superior mechanical properties, including:
- High Tensile Strength: ADDere parts exhibit impressive tensile strength, making them capable of withstanding significant stress and strain without breaking.
- Fatigue Resistance: The homogeneity and density of ADDere’s LWAM parts enhance their fatigue resistance, allowing them to endure repeated loading and unloading cycles.
- Hardness: ADDere produced metal parts possess high hardness levels, ensuring they can resist wear and tear, even in demanding applications.
Build Material Versatility
ADDere’s LWAM process is compatible with a wide range of metal alloys, including titanium, stainless steel, nickel alloys and aluminum. This versatility allows manufacturers to select the most suitable material for specific applications, ensuring that the end product meets the required strength and performance standards. Whether it’s aerospace components, construction equipment, or oil and gas piping, ADDere delivers high-strength metal parts tailored to many industries.
Strong Performance in Demanding Applications
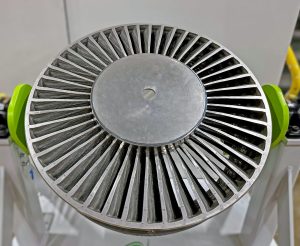
Industries that demand high-performance components are increasingly turning to additive manufacturing for their component manufacturing needs. For example:
- Aerospace: ADDere allows for the production of lightweight yet robust aerospace components that can withstand extreme conditions, such as high temperatures and pressures.
- Off-Highway: ADDere enables the creation of intricate and durable parts that contribute to the dependability of heavy construction equipment.
- Defense: ADDere prints custom metal parts on demand that hold up under the most harsh conditions.
- Petrochemical: ADDere can produce complex and unique piping and mixing channels from high-grade corrosion-resistant nickel alloy metals.
Complex Geometries and Weight Reduction
Traditional manufacturing methods often struggle with creating intricate geometries and complex shapes. However, ADDere excels in this regard. The additive nature of the process enables the production of highly intricate designs, including lattice structures and internal channels. These complex geometries not only enhance strength but also reduce weight, making components more efficient and effective.
Sustainability and Cost-Efficiency
ADDere contributes to sustainability efforts by minimizing material waste. Unlike subtractive methods that result in significant material loss, LWAM uses only the necessary amount of metal wire, reducing waste and lowering production costs. Additionally, the ability to create parts on demand reduces the need for large inventories, leading to cost savings in storage and production.
Let ADDere Print Your Strong Metal Parts
Metal parts produced with ADDere’s Laser Wire Additive Manufacturing process are incredibly strong and durable, making them ideal for a wide range of demanding applications. With exceptional tensile strength, fatigue resistance, and hardness, combined with material versatility and the ability to create complex geometries, LWAM is revolutionizing the future of manufacturing. As industries continue to embrace this advanced technology, we can expect to see even more groundbreaking developments that will shape the future of high-strength metal parts.
The strength of 3D printed metal is undeniably transforming the landscape of modern manufacturing. With its unparalleled strength, material versatility, ability to create complex geometries, and enhanced performance in critical applications, it’s no wonder that industries are embracing this cutting-edge technology.
As we continue to explore the potential of 3D printed metal, we can expect even more groundbreaking advancements that will shape the future of manufacturing. If your manufacturing operation is looking to expand its capabilities and produce strong metal components, then contact us today!