ADDere’s additive manufacturing process and systems are revolutionizing the way we think about manufacturing, offering unprecedented flexibility and innovation in manufacturing complex parts. Among the various additive techniques, laser-wire additive manufacturing (LWAM) and powder-based additive manufacturing (PBAM) stand out for their unique capabilities. Both have their advantages, but there are several compelling reasons why laser-wire is generally superior in most applications.
Build Efficiency & Speed
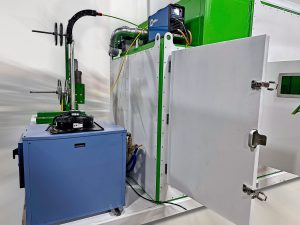
The ADDere Laser-wire additive manufacturing process utilizes a continuous wire feed as the raw material, which can lead to faster deposition rates compared to the layer-by-layer approach of powder-based methods. This translates to build times and enhanced productivity quicker, making it ideal for producing large parts or prototypes on tight deadlines.
ADDere’s metal additive manufacturing systems can significantly reduce the time required to produce complex parts. Traditional manufacturing methods may involve multiple steps and require different machines, leading to longer lead times. In contrast, ADDere’s 3D printing systems and services can produce intricate geometries in a single build process with minimal post-machining, speeding up production cycles. This efficiency can translate into cost savings, particularly for low-volume or custom parts.
Material Utilization & Waste
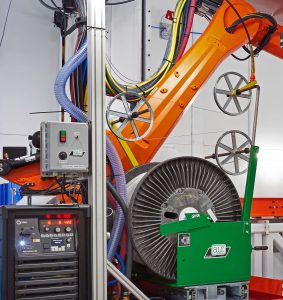
One of the significant advantages of the ADDere laser-wire process is its efficient use of material. With powder-based systems, a considerable amount of unused powder often needs to be sieved and recycled, which can be time-consuming and costly. In contrast, laser-wire systems utilize nearly 100% of the feed material, reducing waste and optimizing resource use. Whereas in a powder-based process, material waste is substantially more and the material is prone to impurities.
Also, printing with laser-wire tends to produce smoother surface finishes with fewer defects, as there is less risk of porosity and other powder-related issues. This can result in fewer post-processing steps, saving time and reducing overall production costs.
Operator Safety & Material Handling
Handling metal powders comes with inherent risks, including inhalation hazards and the potential for dust explosions. Powder-based systems require stringent safety measures and specialized equipment and proper operator PPE to mitigate these risks. On the other hand, laser-wire systems use standard welding wire, which is inherently safer to handle and reduces the need for extensive material handling safety protocols.
Material Costs
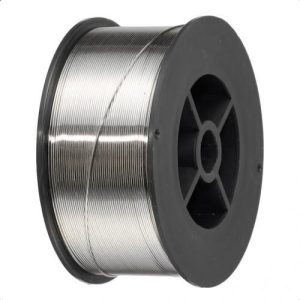
The cost of metal alloy powders can be significantly higher than that of metal wire, primarily due to the manufacturing processes involved in creating fine, uniform metal powder particles. ADDere’s laser-wire additive process essentially uses off-the-shelf welding wire spools. The cost of welding wire ranges from a few hundred dollars a spool to over a thousand depending on the metal alloy. Metal powders, on the other hand, are generally far more expensive than traditional raw wire. The quality of the powder, particle size and specific alloy can significantly influence the cost. However, when compared to traditional subtractive manufacturing methods like CNC machining, which typically results in substantial material waste, additive manufacturing uses only the necessary amount of material.
Applications & Versatility
ADDere’s laser-wire process is versatile and can be applied in various industries. It is particularly useful for repairing parts and components or applying protective coatings, such as in the defense, aerospace and oil & gas industries. It is also well-suited for the fabrication of very large-scale parts, which can be challenging with powder-based due to smaller size limitations.
Environmental Impact
The reduced waste and lower energy consumption associated with ADDere’s laser-wire processes contribute to a smaller environmental footprint than a powder-based solution. With powder requiring a great deal of energy to manufacture and its toxicity to humans, powder additive manufacturing is generally not looked upon as an environmentally sound process. As industries increasingly focus on sustainability, the ecological benefits of laser-wire additive manufacturing become an essential consideration.
How ADDere’s Laser-wire Process is the future of manufacturing
While both laser-wire and powder-based 3D metal printing have their place in manufacturing, laser-wire offers several advantages that can make it a superior choice in many scenarios. Its efficiency, cost-effectiveness, safety and versatility make it an attractive option for manufacturers looking to optimize their large-scale production processes and stay ahead in a competitive market.
ADDere offers several options for manufacturers. We offer three different additive systems each filling a different application, and we also offer an in-house ITAR-compliant printing service for low-run or prototyping parts. If you feel ADDere’s laser-wire additive manufacturing process will enhance your manufacturing process – then contact us today.