Laser Hybrid Welding
Laser Thick Plate Welding with Best-in-Class Process Control
The ADDere laser hybrid welding system uses the unique combination of laser and wire arc welding systems and the closed loop feedback process from our laser-wire additive manufacturing (LWAM) systems. Much like the ADDere additive manufacturing process, ADDere uses a laser to melt the weld keyhole into the metal while using a heated welding wire to fill the weld using conventional welding wire. The process is ideal for heavy-duty welding applications found in shipbuilding, pressure vessels, armor plating and other areas where the thick metal plate is used.
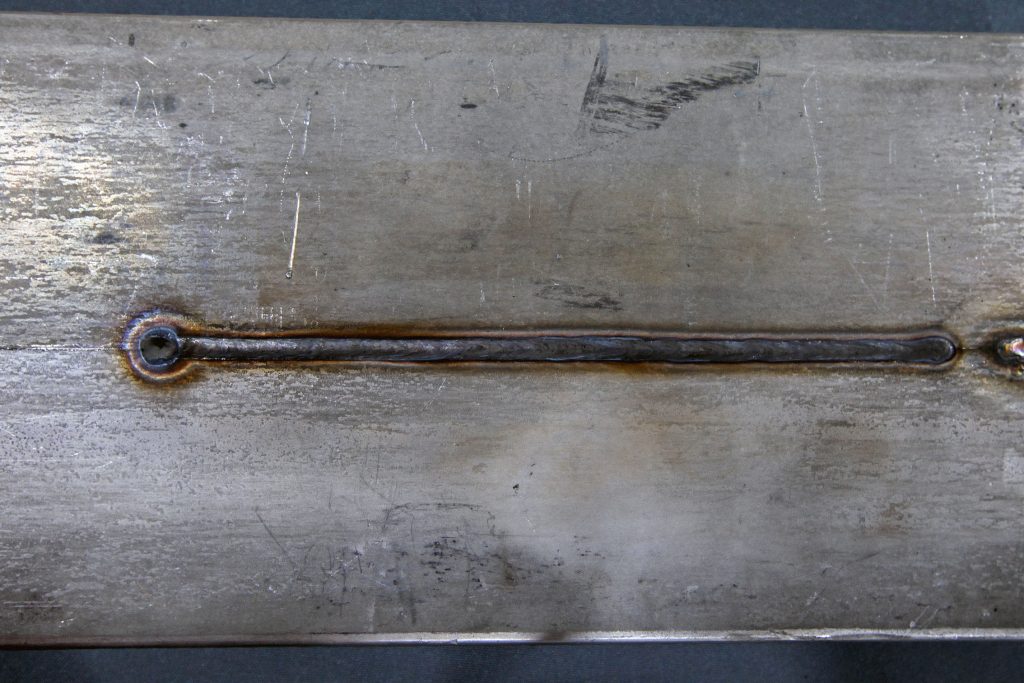
The benefits of the laser hybrid welding system lie in utilizing the laser’s ability to produce a much deeper weld than wire arc welding alone while adding a filler material to strengthen the weld and account for variance in the seam width. This allows for effective single-pass welding in materials that would usually take several passes with conventional wire arc welding alone. With laser hybrid welding, keyhole depths of 25mm in a single pass can be achieved. Adding the ability to weld on both sides effectively doubles that depth for even thicker applications.
The ADDere laser hybrid welding system also offers a much smaller heat-affected zone than other processes. The process offers the benefit of reduced heat absorption in welded materials. This is due to the system’s use of a powerful but precise laser heat source when producing the weld. The finely controlled and localized heat reduces material deformation outside of the weld area. This localization reduces the need for post-weld heat treating to correct bending or warping that develops using wire arc welding or other processes.
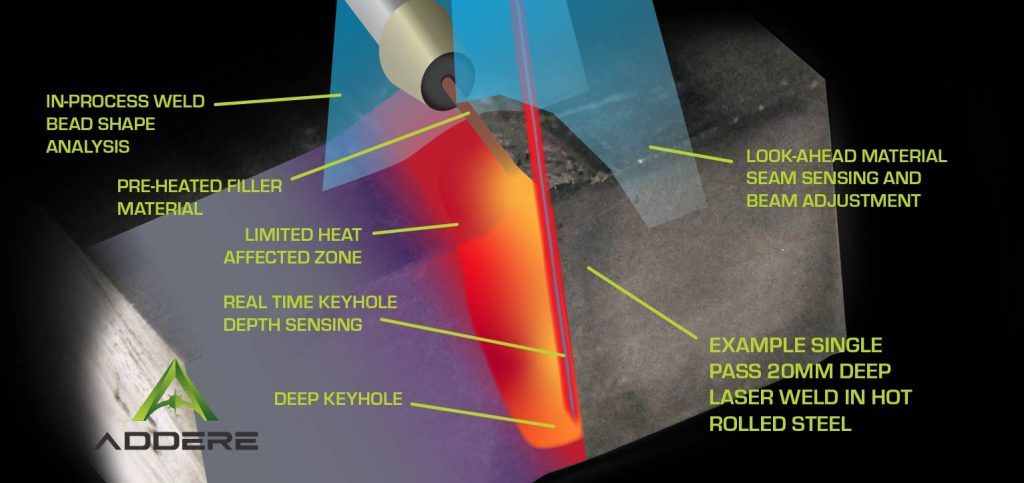
Further, utilizing the ADDere closed-loop feedback system to oversee all aspects of the laser wire welding process helps ensure success in automated heavy plate welding. The proprietary feedback system monitors a variety of weld parameters – including recording the keyhole depth to assessing the finished weld dimensions – in real-time and makes adjustments to the system as needed to guarantee the highest quality welds.
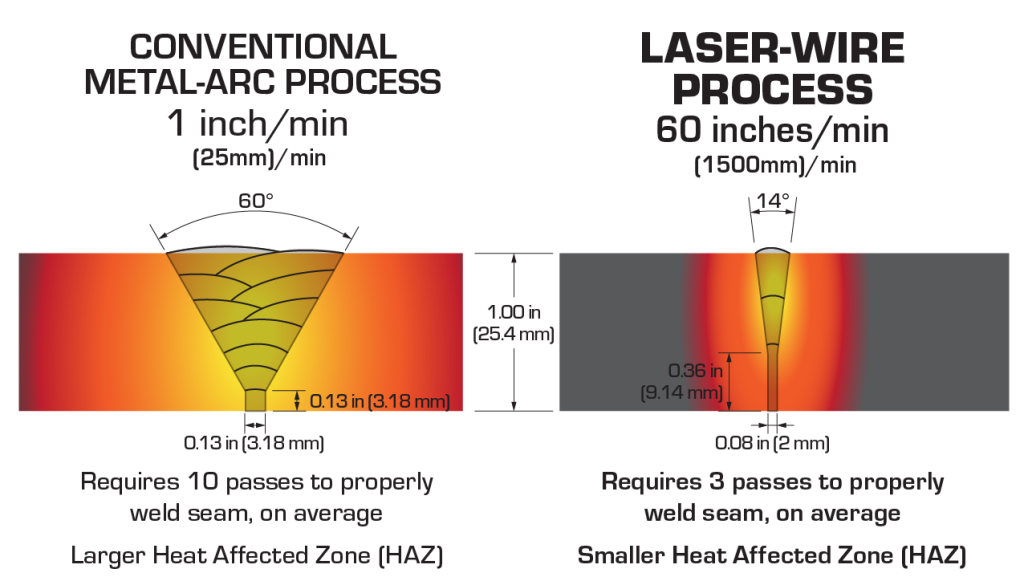
The ADDere laser hybrid welding process is extraordinarily scalable. Combined with the proper robotic automation, systems can be built that could support heavy plate welding up to 40 meters long. Robotic integration of the process also helps ensure a high degree of weld repeatability – which is already exceptional due to the fine-grain control the laser heating inherently provides.
Contact us to learn how laser hybrid welding can fundamentally change the way thick plate welding is done and how we can streamline and enhance your welding process.
do you want to learn more about ADDere's products and services?
What's going on at ADDere
Latest Blog Posts
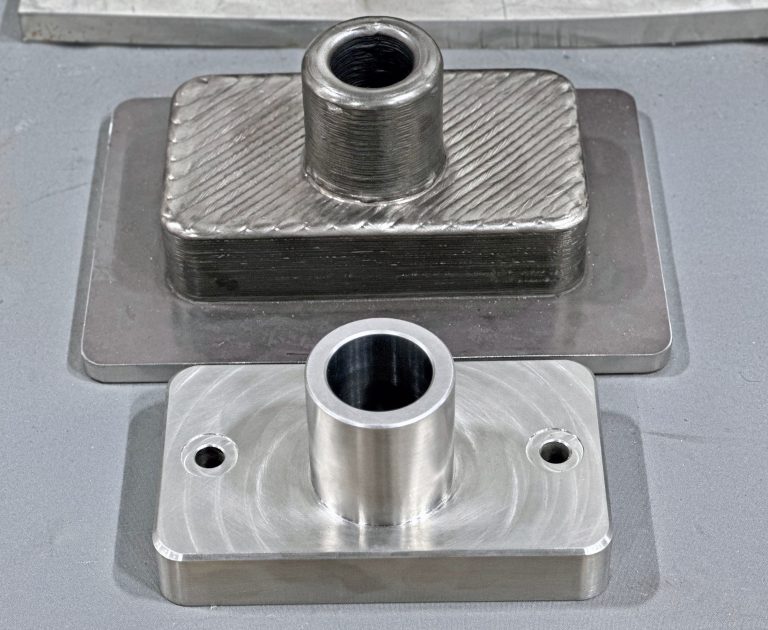
Are 3D Printed Metal Parts Produced with ADDere Strong?
ADDere’s additive manufacturing has revolutionized the production of strong metal-alloy parts, offering unprecedented flexibility and precision. One of the most exciting developments in this field
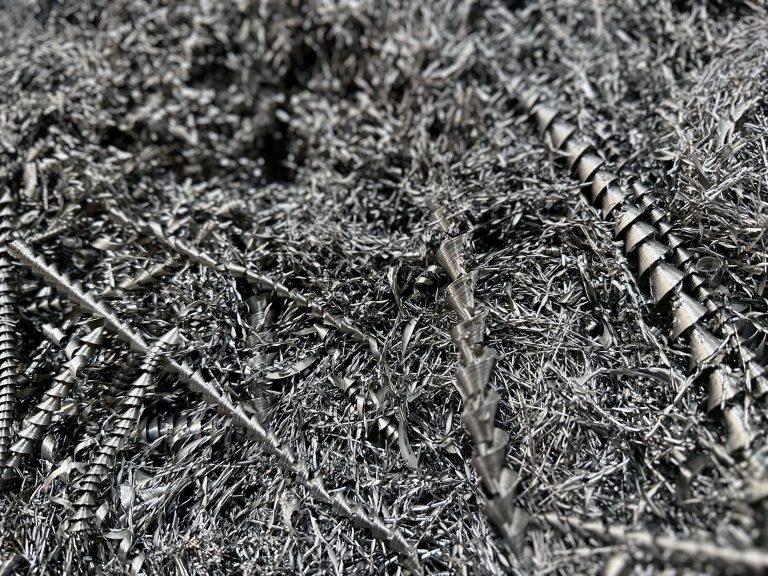
Mitigate Tariffs on Steel by Reshoring Your Manufacturing with ADDere
When it comes to large-scale metal parts manufacturing, ADDere can be a lifesaver for many businesses concerned with high import prices of steel. For decades,
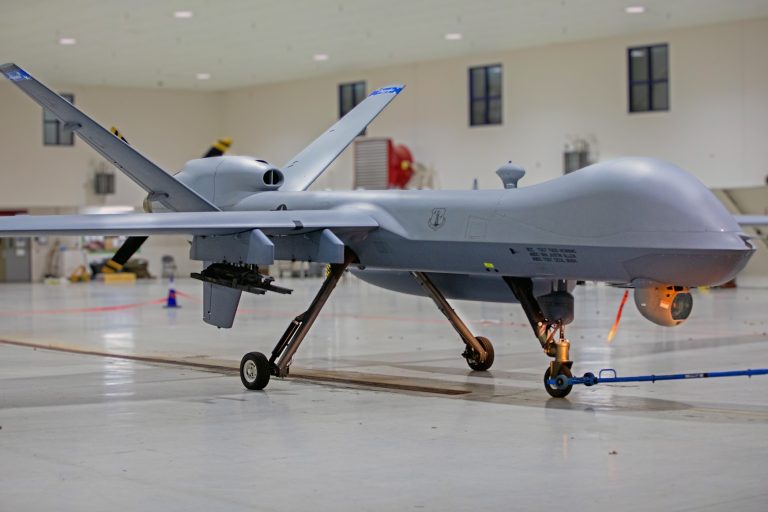
Harnessing ADDere’s Additive Manufacturing Process for Next-Generation Drones
Industrial applications of drones are soaring to new heights in 2025. From utilities and infrastructure inspection to agriculture and defense applications are industries that will
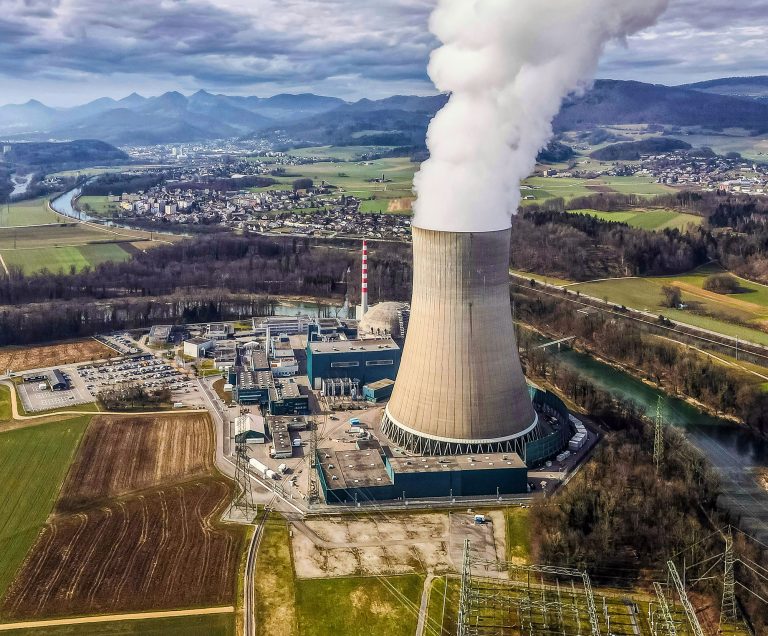
From Concept to Core: How ADDere Transforms Nuclear Reactor Components
Additive manufacturing has been gaining traction in the nuclear energy industry. The development and maintenance of nuclear reactors demand components that meet stringent safety standards
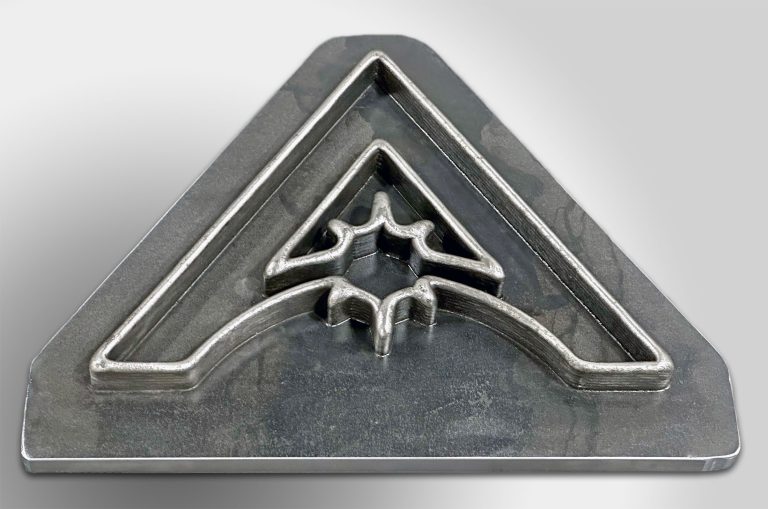
White Paper: The Impact of Additive Manufacturing on Cost, Efficiency & the Future
ADDere’s metal laser-wire additive process is a proven technology for producing complex large-scale metal parts for the defense and aerospace industries. With increasing interest in
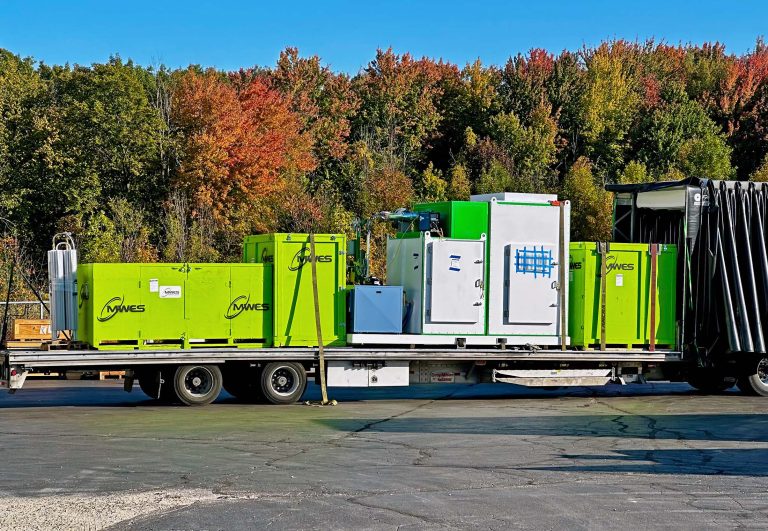
Cost-Benefit Analysis of ADDere’s Additive Manufacturing Process
ADDere’s metal additive manufacturing process has transformed the manufacturing landscape by enabling the production of complex parts with unprecedented precision. Additive manufacturing has evolved from